PDCA
![]() | This article includes a list of references, related reading, or external links, but its sources remain unclear because it lacks inline citations. (March 2008) |
PDCA ("Plan-Do-Check-Act") is an iterative four-step problem-solving process typically used in quality control. It is also known as the Deming Cycle, Shewhart cycle, Deming Wheel, or Plan-Do-Study-Act.
Meaning
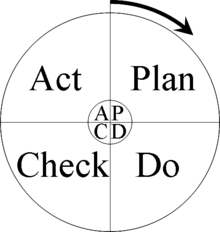
- PLAN
- Establish the objectives and processes necessary to deliver results in accordance with the specifications.
- DO
- Implement the processes.
- CHECK
- Monitor and evaluate the processes and results against objectives and Specifications and report the outcome.
- ACT
- Apply actions to the outcome for necessary improvement. This means reviewing all steps (Plan, Do, Check, Act) and modifying the process to improve it before its next implementation.
About
PDCA was made popular by Dr. W. Edwards Deming, who is considered by many to be the father of modern quality control; however it was always referred to by him as the "Shewhart cycle." Later in Deming's career, he modified PDCA to "Plan, Do, Study, Act" (PDSA) so as to better describe his recommendations.
The concept of PDCA comes out of the Scientific Method, as developed from the work of Francis Bacon (Novum Organum, 1620). The scientific method can be written as "hypothesis" - "experiment" - "evaluation" or Plan, Do, and Check. Shewhart described manufacture under "control" - under statistical control - as a three step process of specification, production, and inspection. Shewhart, 1980, pg. 45. he also specifically related this to the Scientific Method of hypothesis, experiment and evaluation. Shewhart, pg. 48 says that the statistician "must help to change the demand [for goods] by showing...how to close up the tolerance range and to improve the quality of goods." Clearly, Shewhart intended the analyst to take action based on the conclusions of the evaluation. According to Deming Deming, 1986, pg. 88 during his lectures in Japan in the early 1950's the Japanese participants shortened the steps to the now traditional Plan, Do, Check, Act. Deming preferred Plan, Do, Study, Act because 'Study' has connotations in English closer to Shewhart's intent than "Check." In recognition of this perhaps we should make all references to PDSA, not PDCA.
A fundamental principle of the scientific method and PDSA, is iteration - once an hypothesis is confirmed (or negated), executing the cycle again will extend the knowledge further. Repeating the PDSA cycle can bring us closer to the goal, usually a perfect operation and output.
In Six Sigma programs, the PDSA cycle is called "Define, Measure, Analyze, Improve, Control" (DMAIC). The iterative nature of the cycle must be explicitly added to the DMAIC procedure.
PDSA should be repeatedly implemented in spirals of increasing knowledge of the system that converge on the ultimate goal, each cycle closer than the previous. One can envision an open coil spring, with each loop being one cycle of the Scientific Method - PDSA, and each complete cycle indicating an increase in our knowledge of the system under study. This approach is based on the belief that our knowledge and skills are limited, but improving. Especially at the start of a project, key information may not be known; the PDSA - scientific method - provides feedback to justify our guesses (hypotheses) and increase our knowledge. Rather than enter "analysis paralysis" to get it perfect the first time, it is better to be approximately right than exactly wrong. With the improved knowledge, we may choose to refine or alter the goal (ideal state). Certainly, the PDSA approach can bring us closer to whatever goal we choose.
Rate of change -- rate of improvement— is a key competitive factor in today's world. PDSA allows for major 'jumps' in performance ('breakthroughs' often desired in a Western approach), as well as Kaizen (frequent small improvements associated with an Eastern approach). In the United States a PDSA approach is usually associated with a sizable project involving numerous people's time, and thus managers want to see large 'breakthrough' improvements to justify the effort expended. However, the Scientific Method and PDSA apply to all sorts of projects and improvement activities.
The power of Deming's concept is in its apparent simplicity. The concept of feedback in the Scientific Method (aka inductive logic), in the abstract sense, is today firmly rooted in education. While apparently easy to understand, it is often difficult to accomplish on a on-going basis due to the intellectual difficulty of judging one's proposals (hypotheses) on the basis of measured results. Many people have an emotional fear of being shown "wrong," even by objective measurements. To avoid such comparisons, we may instead cite complacency, distractions, loss of focus, lack of commitment, re-assigned priorities, lack of resources, etc.
Problems with PDCA
![]() | This article possibly contains original research. (March 2008) |
PDCA's application was intended for quality control purposes and proposed continuous improvement in quality of products/experiments (Shewart 1939). The simple cycle works well in this application, but it is debatable that it should be applied to major organizational improvement. ISO recognized the need to provide better guidance in this regard and published the ISO standard ISO 9004:2000,which replaced the use of the term continuous improvement with continual improvement. The change is not trivial, it recognizes that organizational quality system performance improvement requires significant effort and needs pauses to consolidate change (hence continual and not continuous improvement) (ISO 9004:2000).
PDCA has an inherent circular paradigm, it assumes that everything starts with Planning. Plan has a limited range of meaning. Shewart intended that experiments and quality control should be planned to deliver results in accordance with the specifications (see meaning above), which is good advice. However, Planning was not intended to cover aspects such as creativity, innovation, invention or Complex Adaptive Systems. In these aspects particularly when based upon imagination, it is often impossible or counterproductive to plan (see referenced Wikipedia pages for why this is so). Hence, PDCA is inapplicable in these situations.
PDCA approaches often do not get to the root cause of a problem, especially in adaptive situations which call for an experiential approach but demand much more rigour in analysis and data collection. An adaptive challenge exists where there are no visible solutions to problems, and can exist, for example in areas where chaos, uncertainty, and ambiguity exists, such as new frontiers, and existing complex systems such as Healthcare.
Do and Act have the same meaning in English. Dictionaries (Shorter Oxford) provide the following relevant definitions:
- Do • verb 1 perform or carry out (an action). 2 achieve or complete (a specified target). 3 act or progress in a specified way. 4 work on (something) to bring it to a required state.
- Act • verb 1 take action; do something. 2 take effect or have a particular effect. 3 behave in a specified way.
The 'Act' in PDCA is meant to be interpreted to have a different meaning to 'Do', otherwise it could be as easily have been PDCD or PACA. In PDCA, 'Act' is meant to apply actions to the outcome for necessary improvement (see meaning above), in other words 'Act' means 'Improve' (applying PDCA to itself could result in PDCI).
References
- Shewhart, Walter Andrew (1939). Statistical Method from the Viewpoint of Quality Control. New York: Dover. ISBN 0-486-65232-7.
- Shewhart, Walter Andrew (1980). Economic Control of Quality of Manufactured Product/50th Anniversary Commemorative Issue. American Society for Quality. ISBN 0-87389-076-0.
- Deming, W. Edwards (1986). Out of the Crisis. MIT Center for Advanced Engineering Study. ISBN 0-911379-01-0.
- International Organisation for Standardisation (ISO) for all ISO standards.
See also
External links
- Note: Before adding your company's link, please read WP:Spam#External link spamming and WP:External links#Links normally to be avoided.