Rapid prototyping
- Rapid (or throwaway) software prototyping also describes a practice in the software development process or application development process and sometimes refers to RAD (rapid application development).

Rapid prototyping is the automatic construction of physical objects using solid freeform fabrication. The first techniques for rapid prototyping became available in the late 1980s and were used to produce models and prototype parts. Today, they are used for a much wider range of applications and are even used to manufacture production quality parts in relatively small numbers. Some sculptors use the technology to produce complex shapes for fine arts exhibitions.
Introduction

Rapid prototyping takes virtual designs from computer aided design (CAD) or animation modeling software, transforms them into thin, virtual, horizontal cross-sections and then creates each cross-section in physical space, one after the next until the model is finished. It is a WYSIWYG process where the virtual model and the physical model correspond almost identically.
With additive fabrication, the machine reads in data from a CAD drawing and lays down successive layers of liquid, powder, or sheet material, and in this way builds up the model from a series of cross sections. These layers, which correspond to the virtual cross section from the CAD model, are joined together or fused automatically to create the final shape. The primary advantage to additive fabrication is its ability to create almost any shape or geometric feature.
The standard data interface between CAD software and the machines is the STL file format. An STL file approximates the shape of a part or assembly using triangular facets. Smaller facets produce a higher quality surface.
The word "rapid" is relative: construction of a model with contemporary methods can take from several hours to several days, depending on the method used and the size and complexity of the model. Additive systems for rapid prototyping can typically produce models in a few hours, although it can vary widely depending on the type of machine being used and the size and number of models being produced simultaneously.
Some solid freeform fabrication techniques use two materials in the course of constructing parts. The first material is the part material and the second is the support material (to support overhanging features during construction). The support material is later removed by heat or dissolved away with a solvent or water.
Traditional injection molding can be less expensive for manufacturing polymer products in high quantities, but additive fabrication can be faster and less expensive when producing relatively small quantities of parts.
Rapid prototyping is now entering the field of rapid manufacturing and it is believed by many experts that this is a "next level" technology.[citation needed]
Technologies
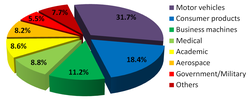
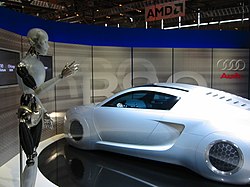
A large number of competing technologies are available in the marketplace. As all are additive technologies, their main differences are found in the way layers are built to create parts. Some are melting or softening material to produce the layers (SLS, FDM) where others are laying liquid materials thermosets that are cured with different technologies. In the case of lamination systems, thin layers are cut to shape and joined together.
As of 2005, conventional rapid prototype machines cost around £25,000. [1]
Prototyping technologies | Base materials |
---|---|
Selective laser sintering (SLS) | Thermoplastics, metals powders |
Fused deposition modeling (FDM) | Thermoplastics, eutectic metals. |
Stereolithography (SLA) | photopolymer |
Laminated object manufacturing (LOM) | Paper |
Electron beam melting (EBM) | Titanium alloys |
3D printing (3DP) | Various materials |
References
Notes
- ^ D. T. Pham, S. S. Dimov, Rapid manufacturing, Springer-Verlag, 2001, ISBN 1-85233-360-X, page 6
Bibliography
- Grenda, E. (2006). The Most Important Commercial Rapid Prototyping Technologies at a Glance.
- Wright, Paul K. (2001). 21st Century manufacturing. New Jersey: Prentice-Hall Inc.
See also
- 3D microfabrication
- 3D printing: faster, more affordable rapid prototyping
- MeshLab, a free and open-source Windows and Linux application for visualizing, processing and converting 3D meshes to or from the STL file format.
- RepRap: a free and open-source multi-material self-replicating rapid prototyping machine
- Solid freeform fabrication: A list of technologies used in rapid prototyping.