User:Shalini srinivasan bcz/sandbox
SPRAY DRYING[edit]

Spray drying is the transformation of feed from a fluid state into a dried particulate form by spraying the feed into a hot drying medium. The first ever detailed description of a drying technique was given as, “The process of simultaneously atomizing and desiccating fluid and solid substances, and its application to the purpose of the exhaustion of moisture from such substances, and for the prevention of destructive chemical change.” This words are now appreciated as “Spray drying”. [1] Spray drying engages liquid atomization, gas/droplet mixing, and drying from liquid droplets. The liquid food is generally preconcentrated by evaporation to economically reduce the water content. The atomized water droplets are usually sprayed downward as a fine spray or mist into a vertical tower or chamber through which hot gases pass downward. As the small droplets make intimate contact with the heated air, they flash off their moisture, become small particles, and drop to the bottom of the tower. Drying is accomplished within a few seconds. The dried product is removed from the bottom of the tower, and the waste gas stream exhausted through a cyclonic dust separator.[1] [2]
History[edit]
Spray drying has its origin in the United States, since the first patented design was registered in 1872. The patent number is 125,406 entitled ‘Improvement in Drying and Concentrating Liquid Substances by Atomizing.’ Samuel Percy first described the principle of spray drying and he is considered to be the inventor of spray drying technology. Spray-drying evolution was directly influenced by World War II, where there was an imperative need to reduce the weight and volume of food and other materials to be carried. It was a significant chronological event in the history of spray drying, monopolizing the process in the dairy industries for continuous production of milk powder. [1] Ever since it was first discovered, the spray-drying technique has been improved concerning its operational design and applications. In fact, the primordial spray dryer devices lacked process efficiency and safety. After overcoming these issues, spray drying became an attractive method for food industry purposes, ending up to be used in milk powder production in the 1920s, remaining one of the most important applications until the current days.
As a result, spray drying has become an industry benchmark, namely in the dairy products’ fabrication. In the post-war period, the spray-drying method continued progressing, reaching the pharmaceutical, chemical, ceramic and polymer industries. [3]The spray drying process is used in a wide range of industrial applications including the manufacture of powdered soaps and detergents, powdered milk, instant coffee, corn starch, fertilizer production, powdered polymer resins and the production of mineral ores and clays. Spray drying stands out from other processes involving liquid drying by its ability to handle feedstock of varying nature, producing flowing powders of specific particle size, high productivity and versatile applications. [1][4]

Spray dryer[edit]
Spray-drying mechanism can be carried out in a pilot-spray dryer developed on a laboratory scale or performed in commercially available instruments. The best spray dryer configuration depends on the purpose for which the instrument is used, that is, the equipment must be compatible with the feedstock solution and meet the processing conditions, which lead to the desirable particle specificity. A spray dryer operates on a convection mode. The principle of working is moisture removal by application of heat to the feed product and controlling the humidity of the drying medium. [5] Air is the heated drying medium; however, if the liquid is a flammable solvent such as ethanol or the product is oxygen-sensitive then nitrogen is used. A spray dryer takes a liquid stream and separates the solute or suspension as a solid and the solvent into a vapor. The solid is usually collected in a drum or cyclone. The liquid input stream is sprayed through a nozzle into a hot vapor stream and vaporized. The most common type of spray dryers are called single effect. There is a single source of drying air at the top of the chamber. In most cases the air is blown in the same direction as the sprayed liquid (co-current). A fine powder is produced, but it can have poor flow and produce much dust. To overcome the dust and poor flow of the powder, a new generation of spray dryers called multiple effect spray dryers have been produced. Instead of drying the liquid in one stage, drying is done through two steps: the first at the top (as per single effect) and the second with an integrated static bed at the bottom of the chamber. The bed provides a humid environment which causes smaller particles to clump, producing more uniform particle sizes, usually within the range of 100 to 300 μm. These powders are free-flowing due to the larger particle size. The fine powders generated by the first stage drying can be recycled in continuous flow either at the top of the chamber (around the sprayed liquid) or at the bottom, inside the integrated fluidized bed.The drying of the powder can be finalized on an external vibrating fluidized bed. [6]
The principal components of a spray dryer are:
- Feed pump - a high pressure pump for introducing liquid into the tower
- Atomizer- a device for atomizing the feed stream
- Air heater- a heated air source with blower
- Air dispenser
- Drying chamber
- Means for exhausting the moist air usually includes a preconcentration step i.e. MVR evaporation
- A secondary collection vessel for removing the dried food from the airstream[7][5]
Spray drying process (1) Atomization. (2) Spray – hot air contact. (3) Evaporation of moisture. (4) Product separation.
Spray drying process[edit]
The process may be described by four major steps namely:
- Atomization of the feed solution.
- Contact of spray with the hot gas.
- Evaporation of moisture.
- Particle separation.[8]
Spray drying nozzle
Atomization[edit]
The spray-drying process is initiated with the feed solution atomization into small droplets due to a decrease of surface tension. This is considered a crucial step for the subsequent phases, namely during the drying chamber exposition. In fact, breaking up the initial solution into many droplets increases their surface area, optimizing therefore the heat and mass transfers between the heated drying gas and the liquid particles. The physical principle behind the atomization transformation process is based on the liquid disintegration phenomenon. [3]The atomization process into droplet form may be accomplished by pressure, centrifugal, electrostatic or ultrasonic energy, using specific devices called atomizers or spray nozzle to disperse the liquid or slurry into a controlled drop size spray. Droplet sizes can range from 20 to 180 μm depending on the nozzle. There are many types of spray nozzles like; single fluid nozzle, two-fluid, rotary disk etc. The two main types of nozzles are high pressure single fluid nozzle (50 to 300 bars) and two-fluid nozzles: one fluid is the liquid to dry and the second is compressed gas (generally air at 1 to 7 bars).The most common of these are rotary disk and single-fluid high pressure swirl nozzles. Alternatively, for some applications two-fluid or ultrasonic nozzles are used. [6]
Contact of spray with air[edit]

Atomized droplets are exposed to a hot gas within the drying chamber, resulting in first rapid moisture evaporation. Usually, this drying gas is heated (and filtered) atmospheric air, although in some cases there is a need to use other inert gases to avoid eventual instabilities between the gas and the droplets. The drying chamber’s size and shape should be consistent with the spray dryer setup, that is, it should be chosen according to the used atomizer and the pretended particle properties. Thus, there are different sized drying chambers (smaller or taller), though they should be big enough to guarantee that particles have the necessary time to dry before reaching the chamber’s walls (otherwise they would deposit in the chamber walls, which is undesirable). The majority of vertical chambers are cylindrical, ending with an inverted cone on its base. There are different drying chamber configurations, in which the flow pattern between the hot gas and the spray of droplets is distinct.
i) Co-current flow: Both the atomized spray and the heated gas enter at the top of the drying chamber, flowing through it in the same direction.
ii) Counter-current flow: Spray and hot gas are introduced at opposite ends of the chamber, being the atomizer positioned at its top and the air supplied from the bottom.
iii) Mixed flow: Combines both co-current flow and counter-current flow, that is, atomized droplets are fed from the bottom of the chamber in counter-current relative to the downward streamline of the drying gas which is supplied from the top.[8]
Evaporation of moisture[edit]
As soon as the aerosol droplets come in contact with the drying medium within the chamber, they undergo evaporation and solute condensation, resulting in solvent removal. This phenomenon reflects a heat and mass balance problem driven by the difference between the solvent’s vapor pressure and its partial pressure toward a gas phase. Thus, the hot gas temperature triggers a heat exchange from it to the droplets, whereas the vapor pressure difference causes a moisture transfer in the opposite direction. As a result, dried particles are obtained. In order to achieve a successful droplet-to-particle conversion, an optimization of the process conditions is required.
Particle separation[edit]
Once the droplet-to-particle conversion is concluded, it is necessary to collect the dried particles. This implies a separation procedure, in which the dried particles are disassociated from the drying gas. Such separation occurs general in two phases, called primary and second separation. In the primary separation, the dense particles are recovered at the conical bottom of the drying chamber, as they settle on it. On the second separation, the finest or smallest particles are transferred to external devices, where they are separated from the humid air. The most common dry collectors include the cyclone separator, the bag filter and the electrostatic precipitator; equipment with different efficiencies and which are used according to the size of particles exhausted with the humid gas and the desired characteristics of the final product.
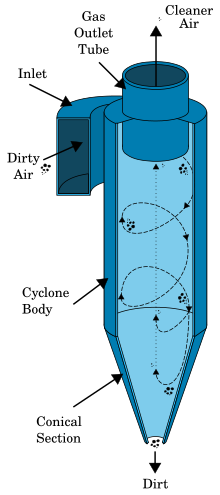
Cyclone separator[edit]
The separation mechanism of the cyclone separator is based on centrifugal force. This device presents a cylindrical upper part, the barrel, and a conical part on its bottom, the cone. The streamline of air containing the dried particles coming from the drying chamber is supplied into the cyclone at its top, namely tangentially to the barrel. Then, this streamline follows a downward flow, creating an outer vortex. The high velocities of the outer vortex create a centrifugal force on the particles, allowing the particles-gas stream separation. As soon as the gas reaches the cone, an inner vortex is created in the opposite direction. Thus, the gas is expelled from the cyclone at its top, whereas the particles settle into a collection chamber placed on its bottom.
Bag filter[edit]
Filtration based on bags is extensively used in the spray-drying process. Here, the air streamline containing the dry particles enters the bag filter under pressure or suction by its hopper and is passed through a fabric, which halts the particles path. This means that the dry particles are retained on the bag surface while the clean air passes through it, being expelled from the device. The accumulated particles on the bag surface are then collected due to pulses of compressed air injected in counter-current flow inside the bags.
Electrostatic precipitator[edit]
Electrostatic precipitation is a method of particle collection whose principle is based on electrostatic forces. A high voltage is applied to discharged wires, forming an electric field between them and the collecting plates that constitute the precipitator . As a result, the gas around these wires is ionized, being capable of charging the particle content of the drying air flowing around this area. Due to Columbic forces, the charged particles converge to the collecting plates and thus the air becomes devoid of dust.
Wet scrubbers[edit]
In a spray-drying process, it is usual to find some particles escaping in the air stream after the dry collection. Owing to this, it is quite common to install an additional collecting system after the dry collectors, the wet scrubbers.They present a converging section, a throat (narrowest part) and a divergent section (diffuser). The inlet air carrying fine particles enters the scrubber and is mixed up with the scrubbing liquid (usually water). This mixture flows throughout the converging section, reaching the throat at high velocity. As a result, a spray of droplets is formed with the dust particles entrapped inside them (scrubbing liquid could also be injected at the throat level). Lastly, the fluid content is separated from the clean gas, being the former discharged and the latter released into the atmosphere.[3][8]
Control systems[edit]
The quality and efficiency of the spray drying process is depending on several parameters such as: The pattern of the spray including the distribution of smaller and bigger droplets, the pattern of the air flow in the spray dryer chamber, the inlet air temperature, the feed rate, the inlet air flow rate etc. Apart from the dried product, exhaust air containing evaporated solvent is a product of the drying process, and parameters such as the outlet air temperature of the exhaust air and the relative humidity of the exhaust air are normally used to design the drying process. The outlet temperature is measured during the process and is generally known to be closely related to the condition of the dried product. Thus it is normal practice to control the operation of a spray dryer apparatus on basis of measurements of the outlet air temperature. Two different methods of control are used namely:
- System A:
Maintaining a set outlet air temperature by adjusting the feed rate to the dryer. It maintains the outlet temperature by adjusting the feed rate. It is particularly suitable for centrifugal spray dryers. This control system usually has another control loop, i.e., controlling the inlet temperature by regulating air heater.
- System B:
Maintaining a set outlet temperature by adjusting the inlet air temperature. It maintains the outlet temperature by regulating the air heater and keeping the constant spray rate. This system can be particularly used for nozzle spray dryers, because varying spray rate will result in change of the droplet size distribution for pressure or pneumatic nozzle.[9]
Advantages of spray drying[edit]
1. Product quality and properties can be effectively controlled and maintained through the entire drying operation.
2. Thermolabile products/ pharmaceuticals can be dried at atmospheric pressure and low temperature.
3. Spray dryer permits high- tonnage production in continuous operation adaptable to conventional PLC control (Programmable Logic Controller) and it is relatively simple to operate.
4. Feedstock in solution, slurry, emulsion, paste, and melt form can be dried if pumpable.
5. Corrosion problem is minimal and the selection of materials of construction of spray dryer is simplified since the dried material comes in contact with the equipment surfaces in an anhydrous condition.
6. Spray dryer produces dry powder particles of controllable particle size, shape, form, moisture content, and other specific properties irrespective of dryer capacity and heat sensitivity.
7. Spray dryer handles a wide range of production rates and provides extensive flexibility in its design that is product specification are readily met through the selection of appropriate spray dryer design and its operation from a wide range of available design.
8. It is an energy-intensive equipment because; (i) Specific heat of evaporation can be supplied in a short time. (ii) The temperature difference across the drying chamber is relatively small and (iii) An appreciable amount of heat is lost with exhaust air.
Disadvantages of spray drying[edit]
1. Spray dryer is bulky and also expensive to install.
2. It is difficult to clean after use.
3. It has a low thermal efficiency that is a lot of heat is wasted during operation.
4. Solid materials cannot be dried using spray dryers.
5. Fire hazard may result from product deposit on the drying chamber.
6. It could rupture intact cells due to its high-pressure atomization process, and generally imparts unacceptable degradation in product quality.
7. Low digestibility of few dried components like algae. [7][10]
Applications[edit]
Spray drying is a very widely applied technique used to dry aqueous or organic solutions, suspensions and emulsions in the food, chemical, electronics, pharmaceutical and biopharmaceutical industry.
Chemical industries applies spray drying to manufacture aluminium chlorohydrate, ammonium nitrate, ammonium phosphate, magnesium hydroxide, zinc oxide, zinc sulphate, bleach powders, carbides (titanium, silicon, tantalum, niobium), catalysts for inorganic and organic chemical reactions. Electrical insulating material consists of spray dried aluminium oxide. E.g: phenol-formaldehyde resin, catalysts, PVC emulsion type, amino acids etc.

In Ceramic industries: E.g. aluminum oxide, carbides, iron oxides, kaolin, etc. and in manufacturing dye stuffs and pigments: E.g. chrome yellow, food color, titanium dioxide, paint pigments, etc. In Fertilizer production: E.g. nitrates, ammonium salts, phosphates, etc. Involved in production of Detergent and surface-active agents: E.g. detergent enzymes, bleach powders, emulsifying agents etc.
In Biochemical industries: E.g. algae, fodder antibiotics, yeast extracts, enzymes, etc. For Environmental pollution control: E.g. flue gas desulfurization, black liquor from paper-making etc.[11]
Food industry[edit]
Within the food industry, spray drying is used to prepare a wide range of products, e.g. baby and infant food, instant coffee, dried milk products, tomato paste. Significant applications are:

1. The spray drying of dairy powders are one of the important applications. In general, skim milk powder, full cream milk powder and whey powder form the major dairy powders.
2. Production of food powder with high starch or sugar content.
3. Production of high protein products.
4. Production of encapsulated powder.[12]
Pharmaceutical[edit]
Within pharmaceutical and biopharmaceutical industry spray drying is often selected to transform the active pharmaceutical ingredients in a powder and to manufacture solid dosage forms containing peptides, proteins or poorly water soluble active pharmaceutical ingredients. are spray dried, despite some activity loss (2–10%) during processing.
1. Spray dryer is used in drying pharmaceuticals. For example, antibiotics such as like penicillin, ampicillin, auremycin, streptomycin, terramycin, tetracycline and other blood products, enzymes, vaccines, etc.
2. It is used in the production of excipients and co-processed excipients with increased flowability, compatibility, and tablet disintegration.
3. To improve drug compressibility and reduce capping tendencies in crystals.
4. It is equally used in the preparation of matrix microcapsule containing drug substances and a biodegradable polymer in order to obtain controlled drug release formulation.
5. It is employed in enhancing solubility and dissolution rates of poorly soluble drugs by formation of pharmaceutical complexes or via the development of solid dispersion thus increasing bioavailability.
6. It is used in the production of dry powder formulation/dry powder aerosol and thermolabile materials.[7][11]
Spray drying of Coffee[edit]

Typically the coffee beans chosen for instant coffee production are from the lower end of the quality scale, since many of the subtle flavours and aromas of the more expensive types are lost in the production process. The production of coffee involves three stages.
- Stage One
This stage involves the production of large quantities of freshly brewed coffee using industrial bulk brewers. Freshly ground coffee is put into contact with hot water in industrial brewers until the desired degree of extraction has occurred. The process can either be the drip filter method that many use in the home or an industrial version of the coffee percolator. Much waste product is produced in the initial brewing chambers in the form of used coffee grounds. However these days they are recycled for use in animal foods, used as organic fuels or processed as compost.
- Stage Two
The resulting coffee liquor liquid is then concentrated through an evaporation process where some of the volatile aroma components are removed and stored to be returned later prior to packing. This stage produces a thick more viscous coffee liquid that is then ready for the next stage in the making of spray dried instant coffee.
The concentrated liquid coffee is then sent to the spray- drying tower where it is turned into powder. This is achieved by pumping the coffee concentrate through an atomizer where it is broken into small droplets. These droplets react with the hot drying gases in the tower and lose moisture rapidly. They are are suspended in the drying air and typically separated by centrifugal action.
The powdered coffee produced can however often be too fine to be easily used. Consequently it often undergoes an additional process called agglomeration, which results in a more useable and appealing product. The fine coffee particles are gathered into larger particles using a partial re-hydration process which produces a more visually tempting finished product.[13]
Conclusion[edit]
Even after more than a century of research, spray drying is still a target of study and innovation due to the increasing demand for complex particles with specific characteristics. This is considered a powerful technological process since it brings feasibility to the production of free-flowing particles with well-defined particle size. Besides, bearing in mind the ability to use different feedstocks as well as its high productivity and broad applications, makes this technique more and more attractive to the scientific community. It was noticed that the spray-drying conditions form a network of mutual relationships which have a direct influence on the spray-drying efficiency. The advantages and drawbacks of each parameter should be weighed in order to produce products with desirable characteristics. Such parameters should not be analyzed separately, but rather looked as a complex model, which as a whole contributes to the success of the spray-drying process. The scalability and the cost-effectiveness of this manufacturing process in obtaining dried particles in submicron-to-micron scale favors an increasing variety of applications within the food, chemical, polymeric, pharmaceutical, biotechnology and medical industries. [3]
References[edit]
- ^ a b c d Anandharamakrishnan, C.; S, Padma Ishwarya (2015-07-23). Spray Drying Techniques for Food Ingredient Encapsulation. John Wiley & Sons. ISBN 978-1-118-86407-4.
- ^ "Spray Drying - Process Summary | Food Science". www.uoguelph.ca. Retrieved 2020-07-31.
- ^ a b c d Santos, Daniel; Maurício, Ana Colette; Sencadas, Vitor; Santos, José Domingos; Fernandes, Maria H.; Gomes, Pedro S. (2017-12-20). "Spray Drying: An Overview". Biomaterials - Physics and Chemistry - New Edition. doi:10.5772/intechopen.72247.
- ^ "The invention of spray drying". History of Food Processing. 2013-05-19. Retrieved 2020-07-31.
- ^ a b "Spray Drying - Process Summary | Food Science". www.uoguelph.ca. Retrieved 2020-07-31.
- ^ a b "Spray drying", Wikipedia, 2020-01-23, retrieved 2020-07-31
- ^ a b c "Spray Dryer: Operating principles, Process layout, Uses, advantag". Pharmapproach.com. 2016-01-11. Retrieved 2020-07-31.
- ^ a b c K, Masters (1991). Spray Drying Handbook, 5th ed.,. London: Longman Scientific & Technical. pp. 120-121 and 375-371.
- ^ [1], "Method of controlling a spray dryer apparatus by regulating an inlet air flow rate, and a spray dryer apparatus", issued 2006-12-22
- ^ Show, Kuan-Yeow; Yan, Yue-Gen; Lee, Duu-Jong (2019-01-01), Pandey, Ashok; Chang, Jo-Shu; Soccol, Carlos Ricardo; Lee, Duu-Jong (eds.), "Chapter 7 - Algal biomass harvesting and drying", Biofuels from Algae (Second Edition), Biomass, Biofuels, Biochemicals, Elsevier, pp. 135–166, ISBN 978-0-444-64192-2, retrieved 2020-07-31
- ^ a b Jain, Manu; Ganesh, Lohare; Manoj, Bari; Randhir, Chavan; Shashikant, Barhate; Chirag, Shah (2012-04-03). "Spray Drying in Pharmaceutical Industry: A Review". 4: 74–79.
{{cite journal}}
: Cite journal requires|journal=
(help) - ^ Woo, M. W.; Bhandari, B. (2013-01-01), Bhandari, Bhesh; Bansal, Nidhi; Zhang, Min; Schuck, Pierre (eds.), "2 - Spray drying for food powder production", Handbook of Food Powders, Woodhead Publishing Series in Food Science, Technology and Nutrition, Woodhead Publishing, pp. 29–56, ISBN 978-0-85709-513-8, retrieved 2020-07-31
- ^ "Coffee Spray Drying". www.austfood.com. Retrieved 2020-07-31.
Bibliography[edit]
- Patel, R.P.; Patel, M.P.; Suthar, A.M. (2009-01-01). "Spray drying technology: An overview". Indian Journal of Science and Technology. 2: 44–47. doi:10.17485/ijst/2009/v2i10/30719.
- Onwulata, C. "Encapsulated and Powdered Foods", Food Science and Technology; CRC Press. (2005) https://books.google.co.in/books?id=VzzIzTQHALMC