Polycrystalline silicon
This article needs additional citations for verification. (February 2008) |
Crystalline silicon is a material consisting of one or more small silicon crystals. It is different from the amorphous silicon, used for thin films.
Monocrystalline
Semiconductor grade (also solar grade) polycrystalline silicon is converted to "single crystal" silicon - meaning that the randomly associated atoms of silicon in "polycrystalline silicon" are converted to large "single" crystals of silicon. Single crystal silicon is used to manufacture 99% of all electronic devices.[citation needed] The devices are used in watches, refrigerators, microwaves, televisions, radios, communications equipment such as cell phones, and controls for cars, ships, aircraft, missiles, and atomic weapons.
A single crystal, also called monocrystal, is a crystalline solid in which the crystal lattice of the entire sample is continuous and unbroken to the edges of the sample, with no grain boundaries. The opposite of a single crystal sample is an amorphous structure where the atomic position is limited to short range order only. In between the two extremes exist polycrystalline and paracrystalline phases, which are made up of a number of smaller crystals known as crystallites. Because of a variety of entropic effects on the microstructure of solids, including the distorting effects of impurities and the mobility of crystallographic defects and dislocations, single crystals of meaningful size are exceedingly rare in nature, and can also be difficult to produce in the laboratory under controlled conditions (see also recrystallisation).
Polycrystalline silicon

Polycrystalline silicon (or semicrystalline silicon, polysilicon, poly-Si, or simply poly in context) is a material consisting of multiple small silicon crystals.
Polycrystalline silicon can be as much as 99.9999999% pure.[citation needed] Silicon is most often companioned with oxygen to form sand. When the oxygen is stripped from the silicon, crude polycrystalline silicon remains. Ultra-pure poly is used in the semiconductor industry, starting from poly rods that are five to eight feet in length.
In microelectronic industry (semiconductor industry), poly is used both at the macro-scale and micro-scale (component) level.
At the macro scale, polysilicon is used as a raw material entering a process in which single crystals are grown (see Czochralski process, Bridgeman technique, Float-zone silicon).
At the component level, polysilicon has long been used as the conducting gate material in MOSFET and CMOS processing technologies. For these technologies it is deposited using low-pressure chemical-vapour deposition (LPCVD) reactors at high temperatures and is usually heavily N or P-doped.

More recently, intrinsic and doped polysilicon is being used in large-area electronics as the active and/or doped layers in thin-film transistors. Although it can be deposited by LPCVD, plasma-enhanced chemical vapour deposition (PECVD), or solid-phase crystallization (SPC) of amorphous silicon in certain processing regimes, these processes still require relatively high temperatures of at least 300°C. These temperatures make deposition of polysilicon possible for glass substrates but not for plastic substrates. The drive to deposit Polycrystalline silicon or poly-Si on plastic substrates is powered by the desire to be able to manufacture digital displays on flexible screens. Therefore, a relatively new technique called laser crystallization has been devised to crystallize a precursor amorphous silicon (a-Si) material on a plastic substrate without melting or damaging the plastic. Short, high-intensity ultraviolet laser pulses are used to heat the deposited a-Si material to above the melting point of silicon, without melting the entire substrate. The molten silicon will then crystallize as it cools. By precisely controlling the temperature gradients, researchers have been able to grow very large grains, of up to hundreds of micrometers in size in the extreme case, although grain sizes of 10 nanometres to 1 micrometre are also common. In order to create devices on polysilicon over large-areas however, a crystal grain size smaller than the device feature size is needed for homogeneity of the devices. Another method to produce poly-Si at low temperatures is metal-induced crystallization where an amorphous-Si thin film can be crystallized at temperatures as low as 150C if annealed while in contact of another metal film such as aluminium, gold, or silver

One major difference between polysilicon and a-Si is that the mobility of the charge carriers can be orders of magnitude larger and the material also shows greater stability under electric field and light-induced stress. This allows more complex, high-speed circuity to be created on the glass substrate along with the a-Si devices, which are still needed for their low-leakage characteristics. When polysilicon and a-Si devices are used in the same process this is called hybrid processing. A complete polysilicon active layer process is also used in some cases where a small pixel size is required, such as in projection displays.
Polysilicon is a key component for integrated circuit and central processing unit manufacturers such as AMD and Intel.
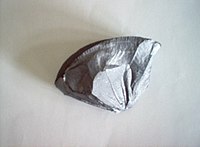
Solar panel
Polycrystalline silicon is also a key component of solar panel construction. The photovoltaic solar industry is growing rapidly but is likely going to be very limited in 2006-2008 due to severe shortages and allocations of the polysilicon material.[1]
For the first time in 2006, over half of the world's supply of polysilicon is being used for production of renewable electricity solar power panels.[2] There are only twelve factories of solar grade polysilicon in the world (in 2008).
Monocrystalline silicon is slightly higher priced and slightly more efficient than multicrystalline.
Upgraded metallurgical-grade silicon
CaliSolar has a project to characterize defects and engineer their distribution within a upgraded metallurgical-grade (UMG) silicon (also known as UMG Si) solar cell to close the efficiency gap between industrial multicrystalline and high-efficiency monocrystalline silicon cells, while preserving the cost advantage of these low-cost, high–volume substrates. The company plans to make cells from 100 percent UMG silicon, which is three orders of magnitude less pure than polysilicon [3].
The project is targeting 18-22% efficient cells (upgraded metallurgical silicon could potentially reach efficiencies of only 0.5 percent less than polysilicon), at manufacturing costs of less than $1 per peak watt, which can potentially be one-sixth that of making polysilicon. [3].
The project is also attempting to build 1,000 tons of UMG silicon capacity for $15 million in six months, while polysilicon plants cost about $100 million for the same capacity and take about three years to build[4] .
SolarWorld has established a joint venture with Scheuten Solarholding to turn dirty metallurgical-grade silicon into high-purity solar-grade silicon. Follows similar ways Dow Corning, Elkem, JFE Steel, and smaller companies Solarvalue and Citizenre [5].
Q-Cells, the world’s largest solar-cell manufacturer, plans to make cells from the material.
Blue Square Energy (BSE) says it has produced a 14.6% efficient solar cell with its patent-pending Bright Point technology. BSE says the efficiency result is one of the highest in the world on upgraded metallurgical-grade (UMG) silicon and has been verified independently by the National Renewable Energy Laboratory [6].
Manufacturers
Polysilicon
Major polysilicon manufacturers include Hemlock Semiconductor Corporation [7], Wacker Chemie, REC, Tokuyama, MEMC, Mitsubishi (Japan and America) and Sumitomo Corporation, as well as several small sites in China and Russia.
The first 7 companies cover over 75% of the worldwide production capacity of polysilicon (2006).[citation needed]
![]() | This section needs expansion. You can help by adding to it. (June 2008) |
See also
- Low-cost solar cell
- Metallurgical grade silicon
- Monocrystalline silicon
- Nanocrystalline silicon
- Polycrystal
- Photovoltaic cells
- Wafer (electronics)
References
- ^ The Wall Street Journal, A Shortage Hits Solar Power. April 29, 2006.
- ^ Photovoltaics: Getting Cheaper
- ^ a b Calisolar - Home
- ^ Greentech Media | Charting a Path to Low-Cost Solar
- ^ Solar: Doing the Dirty
- ^ http://www.solarindustrymag.com/e107_plugins/content/content.php?content.2138
- ^ Hemlock Semiconductor Corporation
External links
- Crystalline silicon (EERE).
- The US Display Consortium, promoting the development of polycrystalline silicon flat-panel display technologies
- The Coming Boom in Photovoltaic Power
- Alan Joch (November 10, 2006). "Sand Trap: Will the silicon shortage stunt the solar industry's growth?". Plenty Magazine.
- Polycrystalline Silicon Technology - A company that offers technology for polysilicon production
- Polysilicon Plant in India.