Weighing scale
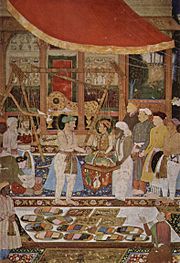
A weighing scale (usually just "scales" in UK and Australian English, or "scale" in US English,) is a measuring instrument for determining the weight or mass of an object. A spring scale measures weight by the distance a spring deflects under its load. A balance compares the unknown weight to a standard weight using a horizontal lever. Weighing scales are used in many industrial and commercial applications, and products from feathers to loaded tractor-trailers are sold by weight. Specialized medical scales and bathroom scales are used to measure the body weight of human beings.
Balance
The balance (also balance scale, beam balance and laboratory balance) was the first mass measuring instrument invented. In its traditional form, it consists of a pivoted horizontal lever of equal length arms, called the beam, with a weighing pan, also called scale, scalepan, or bason (obsolete [1]), suspended from each arm (hence the plural term "scales" for the entire instrument). The unknown mass is placed in one pan, and standard masses are added to the other pan until the beam is as close to equilibrium as possible. In precision balances, a slider weight is moved along a graduated scale. The slider position gives a fine correction to the weight value. Although a balance technically compares weights, not masses, the weight of an object is proportional to its mass, and the standard weights used with balances are usually labeled in mass units.

Balances are used for precision mass measurement, because unlike spring scales their accuracy is not affected by differences in the local gravity, which can vary by almost 0.5%[2] at different locations on Earth. A change in the strength of the gravitational field caused by moving the balance will not change the measured mass, because the moments of force on either side of the balance beam are affected equally.
Very precise measurements are achieved by ensuring that the balance's fulcrum is essentially friction-free (a knife edge is the traditional solution), by attaching a pointer to the beam which amplifies any deviation from a balance position; and finally by using the lever principle, which allows fractional masses to be applied by movement of a small mass along the measuring arm of the beam, as described above. For greatest accuracy, there needs to be an allowance for the buoyancy in air, whose effect depends on the densities of the masses involved.
The original form of a balance consisted of a beam with a fulcrum at its center. For highest accuracy, the fulcrum would consist of a sharp V-shaped pivot seated in a shallower V-shaped bearing. To determine the mass of the object, a combination of reference masses was hung on one end of the beam while the object of unknown mass was hung on the other end (see balance and steelyard balance). For high precision work, the center beam balance is still one of the most accurate technologies available, and is commonly used for calibrating test weights.
To reduce the need for large reference masses, an off-center beam can be used. A balance with an off-center beam can be almost as accurate as a scale with a center beam, but the off-center beam requires special reference masses and cannot be intrinsically checked for accuracy by simply swapping the contents of the pans as a center-beam balance can. To reduce the need for small graduated reference masses, a sliding weight called a poise can be installed so that it can be positioned along a calibrated scale. A poise adds further intricacies to the calibration procedure, since the exact mass of the poise must be adjusted to the exact lever ratio of the beam.
For greater convenience in placing large and awkward loads, a platform can be floated on a cantilever beam system which brings the proportional force to a noseiron bearing; this pulls on a stilyard rod to transmit the reduced force to a conveniently sized beam. One still sees this design in portable beam balances of 500 kg capacity which are commonly used in harsh environments without electricity, as well as in the lighter duty mechanical bathroom "scale" (misnamed, since it is actually a balance). The additional pivots and bearings all reduce the accuracy and complicate calibration; the float system must be corrected for corner errors before the span is corrected by adjusting the balance beam and poise. Such systems are typically accurate to at best 1/10,000 of their capacity, unless they are expensively engineered.
Some high-end mechanical balances also use dials with counterbalancing masses instead of springs, a hybrid design with some of the accuracy advantages of the poise and beam but the convenience of a dial reading. These designs are expensive to produce and have become largely obsolete due to the advent of electronic balances.
Analytical balance

An analytical balance is used to measure mass to a very high degree of precision and accuracy. The weighing pan(s) of a high precision (.01 mg or better) analytical balance are inside a transparent enclosure with doors so that dust does not collect and so any air currents in the room do not affect the balance's operation. The use of a vented balance safety enclosure, which has uniquely designed acrylic airfoils, allows a smooth turbulence-free airflow that prevents balance fluctuation and the weighing of mass down to 1 μg without fluctuations or loss of product. Also, the sample must be at room temperature to prevent natural convection from forming air currents inside the enclosure, affecting the weighing.
Analytical precision is achieved by maintaining a constant load on the balance beam, by subtracting mass on the same side of the beam to which the sample is added. The final balance is achieved by using a small spring force rather than subtracting fixed weights.
Spring scale

In a typical spring scale, the spring stretches (as in a hanging scale in the produce department of a grocery store) or compresses (as in a simple bathroom scale) in proportion to how hard the Earth pulls down on the object. Every spring has a proportionality constant that relates how hard it is pulled to how far it stretches. Some weighing scales such as a Jolly balance (named after Philipp von Jolly who invented the balance about 1874) use a spring with a known spring constant (see Hooke's law) and measure the displacement of the spring by any variety of mechanisms to produce an estimate of the gravitational force applied by the object, which can be simply hung from the spring or set on a pivot and bearing platform. Rack and pinion mechanisms are often used to convert the linear spring motion to a dial reading.
Spring scales measure weight, the local force of gravity on an object, and are usually calibrated in units of force such as newtons or pounds-force. They have two sources of error that balance scales do not; the measured weight varies with the strength of the local gravitational force, by as much as 0.5% at different locations on Earth, and the elasticity of the measurement spring can vary slightly with temperature. Spring scales which are legal for commerce either have temperature compensated springs or are used at a fairly constant temperature, and must be calibrated at the location in which they are used, to eliminate the effect of gravity variations.
Strain gauge scale
In electronic versions of spring scales, the deflection of a beam supporting the unknown weight is measured using a strain gauge, which is a length-sensitive electrical resistance. The capacity of such devices is only limited by the resistance of the beam to deflection. The results from several supporting locations may be added electronically, so this technique is suitable for determining the weight of very heavy objects, such as trucks and rail cars, and is used in a modern weighbridge.
Hydraulic or pneumatic scale
It is also common in high-capacity applications such as crane scales to use hydraulic force to sense weight. The test force is applied to a piston or diaphragm and transmitted through hydraulic lines to a dial indicator based on a Bourdon tube or electronic sensor.
Testing and certification

Most countries regulate the design and servicing of scales used for commerce. This has tended to cause scale technology to lag behind other technologies because expensive regulatory hurdles are involved in introducing new designs. Nevertheless, there has been a recent trend to "digital load cells" which are actually strain-gauge cells with dedicated analog converters and networking built into the cell itself. Such designs have reduced the service problems inherent with combining and transmitting a number of 20 millivolt signals in hostile environments.
Government regulation generally requires periodic inspections by licensed technicians using weights whose calibration is traceable to an approved laboratory. Scales intended for casual use such as bathroom or diet scales may be produced, but must by law be labelled "Not Legal for Trade" to ensure that they are not repurposed in a way that jeopardizes commercial interest. In the United States, the document describing how scales must be designed, installed, and used for commercial purposes is NIST Handbook 44.
Because gravity varies by over 0.5% over the surface of the earth, the distinction between force due to gravity and mass is relevant for accurate calibration of scales for commercial purposes. Usually the goal is to measure the mass of the sample rather than its force due to gravity at that particular location.
Traditional mechanical balance-beam scales intrinsically measured mass. But ordinary electronic scales intrinsically measure the gravitational force between the sample and the earth, i.e. the weight of the sample, which varies with location. So such a scale has to be re-calibrated after installation, for that specific location, in order to obtain an accurate indication of mass.
See Verification and validation for further information
Supermarket/retail scale
These scales are used in the bakery, deli, seafood, meat, produce, and other perishable departments. Supermarket scales can print labels and receipts (in bakery specially), marks weight/count, unit price, total price and in some cases tare, a supermarket label prints weight/count, unit price and total price. Some manufacturers are Goldtech, Adam Equipment, AEW Delford, Hobart Corporation, Bizerba, DIGI/Teraoka, Avery India, Mettler Toledo, CAS, Avery Berkel, Omega Ditron, Ishida and ATP-Instrumentation. Some modern supermarket scales print an RFD tag that can be used to track the item for tampering or returns. In most cases these type of scales have a sealed calibration so that the reading on the display is correct and cannot be tampered with - in the USA the approval is NTEP, for South Africa it is SABS, the UK it is OIML.
Sources of error

Some of the sources of potential error in high-precision balances or scales include the following:
- Buoyancy, because the object being weighed displaces a certain amount of air, which must be accounted for. Some high-precision balances may be operated in a vacuum.
- Error in reference weight
- Air gusts, even small ones, which push the scale up or down
- Friction in the moving components that prevents the scale from reaching equilibrium
- Settling airborne dust contributing to the weight
- Mis-calibration over time, due to drift in the circuit's accuracy, or temperature change
- Mis-aligned mechanical components due to thermal expansion/contraction of components
- Magnetic fields acting on ferrous components
- Forces from electrostatic fields, for example, from feet shuffled on carpets on a dry day
- Chemical reactivity between air and the substance being weighed (or the balance itself, in the form of corrosion)
- Condensation of atmospheric water on cold items
- Evaporation of water from wet items
- Convection of air from hot or cold items
- Gravitational anomalies (i.e. using the balance near a mountain; failing to level and recalibrate the balance after moving it from one geographical location to another)
- Vibration and seismic disturbances; for example, the rumbling from a passing truck
Symbolism
The scales (specifically, a two pan, beam balance) are one of the traditional symbols of justice, as wielded by statues of Lady Justice. This corresponds to the use in metaphor of matters being "held in the balance". It has its origins in ancient Egypt.[citation needed]
See also


- Ampere balance
- Apparent weight
- AutoAnalyzer
- Libra
- Mass versus weight
- Multihead weigher
- Combination weigher
- Nutrition scale
- Roberval Balance
- Steelyard balance
- System suitability test - optional
- Tare weight
- Watt balance
- Weigh house - historic public building for the weighing of goods
- Weigh lock - for weighing canal barges
- Weighbridge - for weighing vehicles (such as trucks) and railcars
Footnotes
- ^ "A Practical Dictionary of the English and German Languages" (1869) p.1069
- ^ Hodgeman, Charles, Ed. (1961). Handbook of Chemistry and Physics, 44th Ed. Cleveland, USA: Chemical Rubber Publishing Co.
{{cite book}}
: Cite has empty unknown parameter:|coauthors=
(help)CS1 maint: multiple names: authors list (link) p.3480-3485
External links
- National Conference on Weights and Measures, NIST Handbook 44, Specifications, Tolerances, And Other Technical Requirements for Weighing and Measuring Devices, 2003
- Analytical Balance article at ChemLab
- HowStuffWorks:Inside a bathroom scale
- Loadcells & Strain Gauges Importance