User:AutumnRho/sandbox
Today's Metal Bellows technology bear little resemblance to the original leather bellows used traditionally in fireplaces and forges. Metal bellows are elastic vessels that can be compressed/extended when a differential pressure is applied to the vessel. When this pressure is released, the bellows will return to its original shape, provided the material has not been stressed past its yield strength. Bellows are used both for their ability to deform under pressure and to provide a hermetic seal that allows movement.
Industries all over the world use metal bellows. They can be found in applications spanning from altitude sensors in airplanes and gas lift valves deep in the sea, to infusion pumps in the human body and double containment pumps in radioactive isotope facilities. Precision bellows technology of the 20th and 21st century is centered on transitioning metal bellows with less demanding applications to be made of rubber or plastic. While bellows can be made of various materials, this article will focus on the different types of metal bellows, their wide assortment of applications, as well as how they are manufactured today.
Types[edit]
There are 2 main types of metal bellows: formed and welded. Hydroformed and rolled bellows are limited to metals with high plastic elongation characteristics, whereas welded bellows may be fabricated from a wider variety of standard and exotic alloys, such as stainless steel and titanium, as well as other high-strength, corrosion-resistant materials. The comparison between the two bellows types generally centers on cost and performance.[1]

Welded Bellows[edit]
Welded bellows (also called edge-welded bellows) are manufactured by welding a number of individually formed diaphragms to each other. A set of welded bellows is referred to as a capsule. The diameter of welded bellows can range from 1/8 inch to 23 inches. Welded bellows can also be round and non-round and are often held to a 1E-10 std cc/sec He leak rate.
Welded bellows work best in compression. Although they can handle up to 20% extension, it dramatically shortens their cycle life.[2]
Welded metal bellows are produced with a lower initial tooling cost and maintain higher performance characteristics compared to formed bellows. The drawback of welded bellows is the reduced metal strength at weld joints, caused by the high temperature of welding.[1] Other advantages to welded bellows include compactness (higher performance in a smaller package), ability to be compressed to solid height with no damage, resistance to nicks and dents, and dramatically greater flexibility.

Formed Bellows[edit]
Formed bellows (also called convoluted bellows or sylphons) can be manufactured in a variety of ways, some of which include reworking tubes, normally produced by deep drawing, with a variety of processes, including cold forming (rolling), and hydroforming. Formed bellows can also be manufactured with a technique called electroforming.
Hydroformed mainly exists to accommodate changes in pressure, vibration, or thermal fluctuations.[3] They generally have a high tooling cost, but, when mass-produced, may have a lower piece price. Hydroformed bellows also have lower performance characteristics due to relatively thick walls and high stiffness.[1]
Electroformed bellows are produced by plating (electroforming) a metal layer onto a model (mandrel), and subsequently removing the mandrel. They can be manufactured with modest tooling costs and thin walls. These thin walls provide bellows with high sensitivity and precision in many exacting applications and can be easily produced in shapes that would be difficult for other types of bellows. Electroformed bellows are also capable of making bellows with diameters as small as 0.02" all the way up to 12".[4] Due to the low tooling cost and short manufacturing cycle, electroforming of bellows is not only an inexpensive manufacturing method, but also a perfect prototyping tool.[5][6]
Applications[edit]
Metal bellows are used in a large number of industrial applications. From pressure sensors in airplanes to hermetic actuators in semiconductor manufacturing, the list of bellows applications are endless.
Aerospace[edit]
Metal bellows are used in the commercial, defense, and space industries. They can be found in military as well as commercial aircraft such as helicopters and jets. Bellows are also used in manned and unmanned spacecraft, launch vehicles, and satellites. In space, they can provide reservoirs for potable water and accumulators to collect wastewater.
The most common products in the aerospace industry are altitude sensors, thermal valves, accumulators, high temperature seals, surge arresters, feedthroughs, coolant reservoirs, volume compensators, and actuators.[7][8][9]
Oil and Gas[edit]
In the oil and gas industry, bellows are used in applications such as exploring the ocean floor, drilling, extracting, transporting, and refining goods. Some of the most common products include compensators, accumulators, high pressure seals, and gas lift valves.[10]
Medical[edit]
Bellows are also used in the medical industry in equipment and devices. Some common applications made with formed bellows include surgical tables, respirators, scanning imaging machines, portable infusion pumps, cat scan machines, and much more.[11] Some examples of edge-welded bellows in the medical industry are pumps, relief valves, couplings, seals, and reservoirs.[12]
Semiconductor[edit]
In the semiconductor industry, bellows are used to help in the manufacturing processes. The semiconductor industry often requires high precision in vacuum-sealed, extremely clean environments. Bellows actuators are often utilized in these situations.[13]
Industrial[edit]
Bellows can be found in industrial sites such as processing plants, medical isotope facilities, and nuclear power plants. Some common applications with bellows include heat exchangers, motors, and hydrogen fuel cells.
Welded bellows are specifically capable of handling extreme environments. Products with bellows include vacuum pumps as well as compressors with radiation monitoring, air sampling and gas handling capabilities. Advanced bellows technology also feature double containment for a redundant hermetic seal. Other products include reservoirs, thermal bypass valves, dynamic seals, and compensators.[14][15][16]
Other[edit]
Here is a list of other common applications with metal bellows:
- Load cells: A load cell deforms if a certain load in the form of a pressure or a strain is imposed on it. This deformation is then detected by a strain gauge through which a low voltage direct current is flowing. The change in voltage is detected and made visible on a control panel. A bellows is mounted over the gauge to protect it from outside influences.
- Vacuum interrupters: For the switching of very high voltages in transformer stations a high vacuum, or high pressure dielectric gas must be maintained around the contacts while in service to mitigate arc formation which would damage the contacts and may prevent safe circuit breaking. Here the bellows allow the contacts to move in and out while maintaining a reliable gas-tight seal.
- Mechanical seals: These are mostly used to close the inside of a pump from the outside world to prevent leakage. For that purpose, a mechanical seal is mounted on the pump shaft. As the pump shaft is turning, there has to be a sealing element consisting of a stationary and a rotating ring. To enforce sufficient pressure on the two rings one is fitted with a spring, the bellows allows the free movement of the spring without leakage. The bellows may be constructed such that it also functions as the spring.
- Pressure gauges: If the pressure of aggressive fluids or gases has to be measured, the gauge has to be isolated from the flow. For critical applications, a diaphragm sealing is used instead of a bourdon tube in the gauge. This gives more security than aggressive media will not leak. The diaphragm is a self-contained sensor, transmitting the displacement to the measuring device.
- Sensors: In this application diaphragm or convoluted bellows are completely sealed and filled with a certain gas. Two electrical poles are penetrating the inside of the bellows. By varying the current of those two poles the temperature inside the bellows can be regulated. The expansion or contraction of the bellows is used as an actuator to control a certain movement.
- Valve sealing: A bellows is used between the housing and the valve stem to seal the inside completely from the outside world. In Europe, this is of particular importance as regulations such as TA Luft prohibit any leakage.
- Couplings for stepper motors and servomotors: The flexible part, capable of compensating for misalignment is made by a bellows. It ensures that there is no angular positioning difference between the two coupling halves. This is essential if the positioning accuracy should be extremely precise.
- Exhaust bellows: Running engines cause self vibration. To compensate for those movements and temperature differences resulting in thermal expansion, bellows are used to connect the exhaust gas pipes to the funnel.
- Piping expansion joint: In this application, a short section of bellows is connected between pipes to absorb thermal movement and vibration, typical in high-vacuum, high-temperature, cryogenic, or high purity systems, and factory-sealed systems that must not allow any gas leakage to or from the interior for a lengthy service life.
Manufacture[edit]
Before metal bellows can be manufactured, the engineer must be given some information. The envelope requirement (maximum/minimum allowable size), differential pressure, temperature ranges, type of environment (salt water/air/vacuum), and cycle life (number of complete cycles before it is unusable) are some examples of specifications a customer would bring to the engineer. All these factors help determine the material type and thickness, number of convolutions, and size of the outer diameter (OD) and inner diameter (ID).[3][5]

Welded Bellows[edit]
A bellows is first manufactured by forming sheet metal (ranging between .001 to .0025 inches thick) into diaphragms. There are typically 3 types of diaphragm designs: 3 Ripple, Flat plate, and Crescent. 3 Ripple designs are the most common type. They have long stroke capabilities, a compact nested length, moderate pressure capability, and high cycle life. Flat plate designs have a stiffer spring rate, good pressure capabilities, and excellent effective area. Effective area is a 2d area of the bellows exposed to the pressure differential. Crescent bellows have a compact nested length as well as good pressure and stroke capabilities.[2]
After the diaphragms are formed, they are welded along the ID. The welding of metal bellows is a microscopic welding process, typically performed under laboratory conditions at high magnification. Different types of welding include micro TIG welding (or GTAW) as well as CO2 laser welding. Two diaphragms welded together form a convolution. Convolutions are then welded together along their OD to create a bellows capsule. Chill rings are commonly inserted in between diaphragms when welded to act as a heat sink. A properly welded bellows should not fail at the weld, but instead at the heat affected zone (HAZ). Welded bellows are commonly made from stainless steels, high nickel alloys, and titanium. Welded bellows are not fabricated from brass because of its fundamentally poor weldability.[2]

Cold Formed Bellows[edit]
Cold formed and deep drawn bellows are manufactured from hollow tubing. This tubing is molded to its desired bellows shape using a press. Since the metal is being stressed during formation, these bellows are often limited to alloys with good elongation – brass being a prime example.
Hydroformed Bellows[edit]
Hydroformed bellows are produced by forcing a metal tube to expand using pressurized fluid inside a bellows-shaped mold, and assume the convoluted shape of the mold.[3][17] Like cold formed bellows, hydroformed material also needs to be an alloy with good elongation.
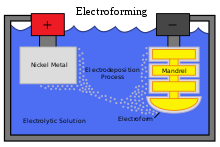
Electroformed Bellows[edit]
Electroformed bellows are produced by plating metal onto a bellows-shaped model (mandrel), and the subsequent mandrel removal by chemical or physical means. Electroformed bellows can be produced of nickel, high-strength alloys, and copper, with walls as small as 0.0002" thin.[4]
Deflections[edit]
The various types of deflections a bellows may see are axial, lateral, angular, torsional, or any combination there of.[18] While axial deflection is the main movement bellows are designed to see, in many cases bellows must be designed to see some combination and level of lateral, angular, and torsional deflection as well. For example, if a bellows was installed with one end fitting slightly higher than another, the bellows will contently experience lateral deflection as well as axial.
Axial deflection is compression or extension along the longitudinal axis of the bellows. In other words, the length of the bellows changes while the axis stays stagnant.
Lateral deflection is when one end of the bellows axis moves while remaining parallel. The lateral offset is the distance between these two axis. This type of deflection has a significant impact on cycle life.[2]
Angular deflection, or angular rotation, is where the axis of the bellows is no longer a straight line, but instead a circular arc. [19]
Torsional deflection is when the bellows stays on its straight line axis, but rotates in a "twisting" motion.
References[edit]
- ^ a b c Sr, Mike Moore (2021-10-12). "The 3 Main Types of Metal Bellows Explained". Retrieved 2022-06-18.
- ^ a b c d "Bellows 101". Senior Metal Bellows. Retrieved 2022-06-16.
- ^ a b c "How Hydroformed Bellows Work | Intran". Intran - The Right Level. 2021-06-01. Retrieved 2022-06-19.
- ^ a b "Seamless Bellows & Assemblies | Metal Bellows Manufacturer | NiCoForm". www.nicoform.com. Retrieved 2022-06-19.
- ^ a b "Edge Welded Metal Bellows vs Formed Bellows Comparison Guide - Flexaseal Engineered Seals and Systems". Flexaseal Engineered Seals and Systems | Mechanical Seals, Seal Support Systems, Seal Repair. 2020-12-22. Retrieved 2022-06-19.
- ^ "Electroformed Metal Bellows | Metal Bellows". MW Components. Retrieved 2022-06-19.
- ^ "Aerospace". Senior Metal Bellows. Retrieved 2022-06-18.
- ^ "Defense". Senior Metal Bellows. Retrieved 2022-06-18.
- ^ "Space". Senior Metal Bellows. Retrieved 2022-06-18.
- ^ "Oil & Gas". Senior Metal Bellows. Retrieved 2022-06-18.
- ^ "Medical Bellows and Their Applications Discussed in Detail - Nabell USA". Retrieved 2022-06-17.
- ^ "Medical". Senior Metal Bellows. Retrieved 2022-06-18.
- ^ "Semiconductor". Senior Metal Bellows. Retrieved 2022-06-18.
- ^ "Industrial". Senior Metal Bellows. Retrieved 2022-06-18.
- ^ "Nuclear". Senior Metal Bellows. Retrieved 2022-06-18.
- ^ "Hydrogen". Senior Metal Bellows. Retrieved 2022-06-18.
- ^ "What is Hydroforming?". Bellows Systems. 2019-01-29. Retrieved 2022-06-19.
- ^ "Types of Deflection". US Bellows Inc. 19 June 2022. Retrieved 19 June 2022.
{{cite web}}
: CS1 maint: url-status (link) - ^ "Definitions". Bellows Systems. Retrieved 2022-06-19.