Chisel: Difference between revisions
m Reverted edits by 202.45.119.37 to last revision by Andy Dingley (HG) |
Tag: repeating characters |
||
Line 37: | Line 37: | ||
A [[Lathe (tool)|lathe]] tool is a woodworking chisel designed to cut wood as it is spun on a lathe. These tools have longer handles for more leverage, needed to counteract the tendency of the tool to react to the downward force of the spinning wood being cut or carved. In addition, the angle and method of sharpening is different, a secondary bevel would not be ground on the tool. |
A [[Lathe (tool)|lathe]] tool is a woodworking chisel designed to cut wood as it is spun on a lathe. These tools have longer handles for more leverage, needed to counteract the tendency of the tool to react to the downward force of the spinning wood being cut or carved. In addition, the angle and method of sharpening is different, a secondary bevel would not be ground on the tool. |
||
Woodworking chisels range from quite small hand tools for tiny details, to large chisels used to remove big sections of wood, in 'roughing out' the shape of a pattern or design. Typically, in woodcarving, one starts with a larger tool, and gradually progresses to smaller tools to finish the detail. One of the largest types of chisel is the slick, used in timber frame construction and wooden shipbuilding. |
Woodworking chisels range from quite small hand tools for tiny details, to large chisels used to remove big sections of wood, in 'roughing out' the shape of a pattern or design. Typically, in woodcarving, one starts with a larger tool, and gradually progresses to smaller tools to finish the detail. One of the largest types of chisel is the slick, used in timber frame construction and wooden shipbuilding. |
||
zzzzzzzzzzzzzzzzzzzzzzzzzzzzzzzzzzzzzzzzzzzzz..................................................................... |
|||
==Metalworking chisels== |
==Metalworking chisels== |
Revision as of 22:54, 16 February 2010

A chisel is a tool with a characteristically shaped cutting edge (such that wood chisels have lent part of their name to a particular grind) of blade on its end, for carving or cutting a hard material such as wood, stone, or metal. The handle and blade of some types of chisel are made of metal or wood with a sharp edge in it.
In use, the chisel is forced into the material to cut the material. The driving force may be manually applied or applied using a mallet or hammer. In industrial use, a hydraulic ram or falling weight ('trip hammer') drives the chisel into the material to be cut.
A gouge, one type of chisel, is used, particularly in woodworking, woodturning and sculpture, to carve small pieces from the material. Gouges are most often used in creating concave surfaces. A gouge typically has a 'U'-shaped cross-section.
Types of Chisels
Chisels have a wide variety of uses. Many types of chisels have been devised, each specially suited to its intended use. Different types of chisels may be constructed quite differently, in terms of blade width or length, as well as shape and hardness of blade. They may have wooden handles attached or may be made entirely of one piece of metal.
Woodworking chisels
Woodworking chisels range from quite small hand tools for tiny details, to large chisels used remove big sections of wood, in 'roughing out' the shape of a pattern or design. Typically, in woodcarving, one starts with a larger tool, and gradually progresses to smaller tools to finish the detail. One of the largest types of chisel is the slick, used in timber frame construction and wooden shipbuilding. According to their function there are many names given to woodworking chisels, such as:
- butt chisel: short chisel with beveled sides and straight edge for creating joints.
- carving chisels: used for intricate designs and sculpting; cutting edges are many; such as gouge, skew, parting, straight, paring, and V-groove.
- corner chisel: resembles a punch and has an L-shaped cutting edge. Cleans out square holes, mortises and corners with 90 degree angles.
- flooring chisel: cuts and lifts flooring materials for removal and repair; ideal for tongue-and-groove flooring.
- framing chisel: usually used with mallet; similar to a butt chisel, except it has a longer, slightly flexible blade.
- slick: a large chisel driven by manual pressure, never struck.
- mortise chisel: thick, rigid blade with straight cutting edge and square sides to make mortises and similar joints.
- paring chisel: has a long blade which is ideal for cleaning grooves and accessing tight spaces.
- skew chisel: has a 60 degree cutting angle and is used for trimming and finishing.
- dovetail chisel: Made specifically for cutting dovetail joints. The difference being the thickness of the body of the chisel, as well as the angle of the edges, permitting easier access to the joint.
Japanese woodworking chisels
The better quality Japanese wood chisels are made from laminated steel. There are different types of metals used in each chisel. The better ones are laminated by hand, over a charcoal fire. The combination of the metals makes a chisel that takes a very sharp edge, and is hard enough to maintain the edge for a long time. This technique produces a tools that have a harder edge, usually a hardness rating of Rockwell 64, compared to their western counterparts of around 62 on the Rockwell scale. There are two basic metals used in these chisels, white steel and blue steel. The names come from the color of the paper the steels are wrapped in. White and blue steel come in vary grades, that vary in carbon content. Both have low levels of impurities. White steel is a simple carbon steel. Blue steel contains alloying elements, and sacrifices some sharpness for edge retention, toughness, and corrosion resistance, although it is not stainless.
Many makers are descendants of the samurai sword makers, once highly respected members of their country, until these swords were outlawed. The chisel makers often turned their attention to chisel and plane makers. Expensive sets have a decorative wood grain look to them which is actually the thin layers of steel being hammered together. The neck of the chisel can be twisted to add to the decorative look of the tool. The handles are often made from an exotic hardwood, such as ebony. The sets usually come in a wooden box, signed by the maker.
Japanese chisels have hollows in the back side, the wider ones having as many as four hollows. These are intended to help in the flattening of the back of the chisels, which is the first step in sharpening a chisel. Once the back side is perfectly flat, and polished to the required degree, the front and side edges need to be addressed. A general rule is any chisel with a hoop, or metal ring at the end of the handle, is designed to be struck with mallet. If it does not have a hoop, it is a paring tool, designed not to be struck with another tool.
Lathe tools
A lathe tool is a woodworking chisel designed to cut wood as it is spun on a lathe. These tools have longer handles for more leverage, needed to counteract the tendency of the tool to react to the downward force of the spinning wood being cut or carved. In addition, the angle and method of sharpening is different, a secondary bevel would not be ground on the tool. Woodworking chisels range from quite small hand tools for tiny details, to large chisels used to remove big sections of wood, in 'roughing out' the shape of a pattern or design. Typically, in woodcarving, one starts with a larger tool, and gradually progresses to smaller tools to finish the detail. One of the largest types of chisel is the slick, used in timber frame construction and wooden shipbuilding. zzzzzzzzzzzzzzzzzzzzzzzzzzzzzzzzzzzzzzzzzzzzz.....................................................................
Metalworking chisels
Chisels used in metal work can be divided into two main categories, hot chisels, and cold chisels. A hot chisel is used to cut metal that has been heated in a forge to soften the metal.
Cold chisel

A cold chisel is a tool made of tempered steel used for cutting 'cold' metals, meaning that they are not used in conjunction with heating torches, forges, etc. Cold chisels are used to remove waste metal when a very smooth finish is not required or when the work cannot be done easily with other tools, such as a hacksaw, file, bench shears or power tools.
The name cold chisel comes from its use by blacksmiths to cut metal while it was cold as compared to other tools they used to cut hot metal. This tool is also commonly referred to by the misnomer coal chisel. Because cold chisels are used to form metal, they have a less-acute angle to the sharp portion of the blade than a woodworking chisel. This gives the cutting edge greater strength at the expense of sharpness.
Cold chisels come in a variety of sizes, from fine engraving tools that are tapped with very light hammers, to massive tools that are driven with sledgehammers. Cold chisels are forged to shape and hardened and tempered (to a blue colour) at the cutting edge.
The head of the chisel is chamfered to slow down the formation of the mushroom shape caused by hammering and is left soft to withstand hammer blows.
The are four common types of cold chisel. These are the flat chisel, the most widely known type, which is used to cut bars and rods to reduce surfaces and to cut sheet metal which is too thick or difficult to cut with tin snips. The cross cut chisel is used for cutting grooves and slots. The blade narrows behind the cutting edge to provide clearance. The round nose chisel is used for cutting semi-circular grooves for oil ways in bearings. The diamond point chisel is used for cleaning out corners or difficult places and pulling over centre punch marks wrongly placed for drilling. Although the vast majority of cold chisels are made of steel, a few are manufactured from beryllium copper, for use in special situations where non-sparking tools are required.
Hardy chisel
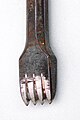
A hardy chisel is a type of hot chisel with a square shank, which is held in place with the cutting edge facing upwards by placing it in an anvil's Hardy hole. The hot workpiece cut is then placed over the hardy, and struck with a hammer. The hammer drives the chisel into the hot metal, allowing it to be snapped off with a pair of tongs.
Stone chisels
Stone chisels are used to carve or cut stone, bricks or concrete slabs. To cut, as opposed to carve, a brick bolster is used; this has a wide, flat blade that is tapped along the cut line to produce a groove, then hit hard in the centre to crack the stone. Sculptors use a spoon chisel, which is bent, with the bezel (cutting edge) on both sides. To increase the force, stone chisels are often hit with club hammers, a heavier type of hammer.
Masonry chisels

Masonry chisels are typically heavy, with a relatively dull head that wedges and breaks, rather than cuts. Normally used as a demolition tool, they may be mounted on a hammer drill, jack hammer, or hammered manually, usually with a heavy hammer of three pounds or more.
Plugging chisel
A Plugging chisel has a tapered edge for cleaning out hardened mortar. The chisel is held with one hand and struck with a hammer. The direction of the taper in the blade determines if the chisel cuts deep or runs shallow along the joint.
See also
Further reading
- Reader's Digest Book of Skills & Tools ISBN 0-89577-469-0
External links