Container chassis
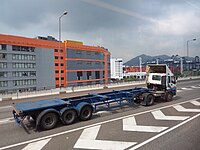
Container chassis, also called intermodal chassis or skeletal trailer, is a specialized semi-trailer, basically a wheeled metal frame, that an intermodal container can be mounted onto for road transport. Chassis are used by truckers to deliver containers between ports, railyards, container depots, and shipper facilities.[1]: 2–3 This type of trucking is sometimes called drayage.






Operation
A container is lifted onto a chassis by a specialized crane, ensuring that the container's corner castings line up with the chassis’ twistlocks (pins). The container is then locked to the chassis by engaging the pins.[2] The length of a chassis determines which container length it can accept. The standard ISO containers are either 20-, 40-, or 45-foot-long. For example, a 40-foot-long chassis is used for a 40-foot-long container. Some chassis can be extended or shortened depending on which container needs to be hauled.[3] In some countries there are other lengths of containers used domestically. For example, in North America there are 53-foot-long containers and 53-foot-long chassis.
Chassis have a kingpin so they can be connected to a semi-tractor. When not hooked up to a tractor, container chassis have a pair of legs called landing gear which can be lowered to support the chassis.[4]
Portable generators, also called gensets, can be mounted (underslung) onto chassis. These gensets are used to power a refrigerated container.[5]
In the US, some chassis, especially 20-foot and 53-foot chassis, have sliding tandems. The tandems are pulled back for heavy containers to comply with federal bridge law weight restrictions.
An identification number is usually stenciled on chassis to keep track of each unit in a fleet. According to ISO 6346, a chassis should have the letter "Z" at the end of its reporting mark. For example, ABCZ-123456 7 would mean the equipment is a chassis, specifically, number 1234567 in the fleet of company ABC.
A variation is the tank container chassis, which are used for portable bulk liquid containers or ISO tank containers. They are characteristically longer and have lower deck height then standard chassis, ideal for transporting constantly shifting payloads. These chassis can also be fitted with additional accessories including: lift kits to facilitate product discharge, hose tubes, and hi/lo kits to carry two empty tanks. The tank chassis has evolved over the years to accommodate greater payload weights. They come in tandem axle, spread axle, tri-axle, and hi/lo combo configurations.
Logistics
United States
In the US, there are two main types of container terminal operations. The first is called a "grounded" or "lift" terminal. At these terminals, containers are stacked on the ground. When picking up a container from a grounded terminal, drivers need to bring a chassis with them or find one somewhere in the terminal. A chassis split is when the chassis and container are in different locations. Once they have a chassis, the driver takes it to where their container is stacked so the yard personnel can mount the container.
The other type of terminal is called "wheeled". Terminal personnel place each container on a chassis and park it before truckers arrive. When truckers arrive, they hook up to the chassis holding their container and drive away. If drivers wish to use a different chassis, they need to get a flip.[6]
When the steamship line is buying the drayage service (called "store door moves" or carrier haulage), they typically have a requirement for the drayage provider to use a particular chassis pool to complete the job.[7]: 26 [8][9] A chassis pool is a fleet of chassis that are available to truckers for rental and return at specific locations. When a driver enters or exits a container terminal with a pool chassis, the check-in kiosk at the terminal entrance sends a record of the event via EDI to the chassis pool company. This allows the chassis pool company to determine which trucking company is using a chassis and when the chassis was picked up or returned. Based on this data, the chassis pool company can create a chassis usage invoice. With carrier haulage, if the drayage provider uses their own private chassis or a pool other than specified by the steamship line, they are usually solely responsible for any incurred costs.[10].
Other countries
In most countries other than the US, truckers own or long-term lease container chassis—steamship lines have no influence on chassis.[1]: 1 [11]
Shortages
In the United States, container chassis shortages are a chronic problem, especially during peaks in freight volume.[12] There are several causes of chassis shortages, but a common problem is excessive off-terminal dwell time. Off-terminal dwell time is the length of time a shipper keeps a chassis/container at their premises. Long dwell times cause shortages at ports and rail ramps where incoming containers need to be loaded onto chassis.[13][14]
See also
References
- ^ a b National Academies of Sciences, Engineering, and Medicine. (2012). Guidebook for Assessing Evolving International Container Chassis Supply Models. Washington, DC: National Academies Press. doi:10.17226/22682. ISBN 978-0-309-25863-0.
{{cite book}}
: CS1 maint: multiple names: authors list (link) - ^ Hildebrand, Michael; Noll, Gregory; Hand, William (2018). Intermodal Container Emergencies (2nd ed.). Burlington, MA: Jones & Bartlett Learning. p. 69.
- ^ Muller, Gerhardt (1989). Intermodal Freight Transportation. Eno Foundation for Transportation. p. 113.
- ^ "Containerisation International Year Book". Containerisation International Year Book. London: National Magazine Company. 1971. Retrieved December 22, 2020.
- ^ Filina-Dawidowicz, L.; Santos, T.; Guedes Soares, C. (2016). "Refrigerated cargo handling: Demand and requirements for Portuguese ports". In Guedes Soares, C.; Santos, T. (eds.). Maritime Technology and Engineering 3. Vol. 1. Leiden, The Netherlands: CRC Press. p. 63. ISBN 978-1-138-03222-4.
- ^ Fact Finding 28: The Memphis Supply Chain Innovation Team. A Single Gray Chassis Pool Fosters Fluid Commerce and Improves Supply Chain Velocity (PDF) (Report). p. 2. Retrieved December 29, 2020.
truckers do not have a choice on chassis provisioning when rail operators have a mounted operational procedure. Containers are available as a mounted unit; shippers and truckers must take the unit as tendered or wait in line for a flip fee to move that container onto another chassis.
{{cite report}}
: CS1 maint: numeric names: authors list (link) - ^ U.S. Container Port Congestion & Related International Supply Chain Issues: Causes, Consequences & Challenges (PDF) (Report). Federal Maritime Commission. July 2015. Retrieved December 29, 2020.
- ^ Mongelluzzo, Bill (June 13, 2019). "Chassis 'utility' model proposed for ports, hubs". JOC.com. Retrieved December 30, 2020.
'Carriers bought the chassis and gave them away for free to attract business,' Rooney said. Then, carriers went almost full circle by renting back the chassis from the equipment providers and offering them at discounted rates, once again to attract business, he said.
- ^ Ashe, Ari (May 30, 2018). "US truckers, shippers frustrated with chassis splits, shortages". JOC.com. Retrieved December 23, 2020.
'in Memphis, we run a TRAC pool and then we contribute to the CCM pool. If we have assets devoted to the TRAC pool for the steamship line for an agreed upon rate, that's the asset the motor carrier needs to use.'
- ^ "Hapag-Lloyd Chassis Program – USA Chassis Provider Summary - January Update - Chassis Program Update".
In cases where Hapag-Lloyd is responsible for chassis usage, we will only accept usage from the above providers and pools. If these providers are not used, the trucker will be charged directly, regardless of the terms of chassis provision.
- ^ "Changing U.S. Intermodal Chassis Operations". OCEMA. Retrieved January 8, 2021.
- ^ "Long tail of US chassis shortage snaps shippers". JOC.com. January 22, 2019. Retrieved December 23, 2020.
The container chassis shortage ranks with the truck driver shortage as a perennial issue that returns to disrupt supply chains whenever freight demand surges.
- ^ Ozkan, Utku (October 9, 2020). "WHY THERE IS A CHASSIS SHORTAGE AT THE PORTS OF LOS ANGELES AND LONG BEACH". More Than Shipping. Retrieved December 22, 2020.
- ^ Mongelluzzo, Bill (July 23, 2020). "Chassis equipment issues reemerge at LA–LB port complex". JOC.com. Retrieved December 22, 2020.
- Further reading
- O'Brien, Thomas; Reeb, Tyler; Kunitsa, Annette (February 2016). Mitigating Urban Freight Through Effective Management of Truck Chassis (PDF) (Technical report). METRANS Transportation Center.
- National Academies of Sciences, Engineering, and Medicine. (2011). "Chapter 8: Container Chassis Supply Time and Delays". Truck Drayage Productivity Guide. Washington, DC: National Academies Press. doi:10.17226/14536. ISBN 978-0-309-15552-6.
{{cite book}}
: CS1 maint: multiple names: authors list (link)
External links
- How truckers can avoid a bad dray day – Six tips for truckers about chassis pools
- At Ag Exporters’ Meeting, the Chassis Debate Rages On – Discussion about the two types of chassis pools, co-op and proprietary
- Athearn HO scale chassis – Model Railroading magazine, June 1999
- RR Rolling Stock Category: Chassis – Picture archives of intermodal chassis in US