Wind turbine design: Difference between revisions
Tag: repeating characters |
|||
Line 166: | Line 166: | ||
The foundations for a conventional [[structural engineering|engineering structure]] are designed mainly to transfer the vertical [[Structural load|load]] (dead weight) to the ground, this generally allows for a comparatively unsophisticated arrangement to be used. However in the case of wind turbines, due to the high wind and environmental loads experienced there is a significant horizontal load that needs to be accounted for. |
The foundations for a conventional [[structural engineering|engineering structure]] are designed mainly to transfer the vertical [[Structural load|load]] (dead weight) to the ground, this generally allows for a comparatively unsophisticated arrangement to be used. However in the case of wind turbines, due to the high wind and environmental loads experienced there is a significant horizontal load that needs to be accounted for. |
||
This loading regime causes large [[torque|moment loads]] to be applied to the foundations of a wind turbine. As a result, considerable attention needs to be given when designing the footings to ensure that the turbines are sufficiently restrained to operate efficiently.<ref>Cox, J. A., & Jones, C. (2010). Long-Term Performance of Suction Caisson Supported Offshore Wind Turbines. Bristol: University of Bristol.</ref> In the current Det Norske Veritas (DNV) guidelines for the design of wind turbines the angular deflection of the foundations are limited to 0.5°.<ref>{{cite book |author=Det Norske Veritas|title=Guidelines for Design of Wind Turbines |publisher=Det Norske Veritas |location=Copenhagen |year=2001 |pages= |isbn= |oclc= |doi= |accessdate=}}</ref> |
This loading regime causes large [[torque|moment loads]] to be applied to the foundations of a wind turbine. As a result, considerable attention needs to be given when designing the footings to ensure that the turbines are sufficiently restrained to operate efficiently.<ref>Cox, J. A., & Jones, C. gggggggggggggggggggggggggggggggggggg(2010). Long-Term Performance of Suction Caisson Supported Offshore Wind Turbines. Bristol: University of Bristol.</ref> In the current Det Norske Veritas (DNV) guidelines for the design of wind turbines the angular deflection of the foundations are limited to 0.5°.<ref>{{cite book |author=Det Norske Veritas|title=Guidelines for Design of Wind Turbines |publisher=Det Norske Veritas |location=Copenhagen |year=2001 |pages= |isbn= |oclc= |doi= |accessdate=}}</ref> |
||
[[Scale model]] tests using a 50[[g-force|g]] [[centrifuge]] are being performed at the [[Technical University of Denmark]] to test [[monopile foundation]]s for offshore wind turbines at 30-50m water depth.<ref name="ing50g">Rasmussen, Daniel. [http://ing.dk/artikel/113038-centrifuge-paa-dtu-tester-moellefundamenter-ved-50-g Wind turbine foundations at 50g] (in Danish) ''Ing.dk'', 26 October 2010. [http://ing.dk/artikel/113041-se-dtus-centrifuge-skabe-50-g 6minute Video] Retrieved: 25 November 2010.</ref> |
[[Scale model]] tests using a 50[[g-force|g]] [[centrifuge]] are being performed at the [[Technical University of Denmark]] to test [[monopile foundation]]s for offshore wind turbines at 30-50m water depth.<ref name="ing50g">Rasmussen, Daniel. [http://ing.dk/artikel/113038-centrifuge-paa-dtu-tester-moellefundamenter-ved-50-g Wind turbine foundations at 50g] (in Danish) ''Ing.dk'', 26 October 2010. [http://ing.dk/artikel/113041-se-dtus-centrifuge-skabe-50-g 6minute Video] Retrieved: 25 November 2010.</ref> |
Revision as of 14:56, 14 February 2011

Wind turbine designs are utilized to create wind turbines that exploit wind energy.[1] A wind turbine installation consists of the necessary systems needed to capture the wind's energy, point the turbine into the wind, convert mechanical rotation into electrical power, and other systems to start, stop, and control the turbine.
This article covers the design of horizontal axis wind turbines (HAWT) since the majority of commercial turbines use this design. Contrary to popular belief, considerable attention should be given to the structural and foundation design of HAWTs. This is mainly due to the disproportionate amount that is spent on the foundations as a percentage of the total project cost.
Design specification
The design specification for a wind-turbine will contain a power curve and guaranteed availability. With the data from the wind resource assessment it is possible to calculate commercial viability.[1] The typical operating temperature range is −20 to 40 °C (−4 to 104 °F). In areas with extreme climate (like Inner Mongolia or Rajasthan) specific cold and hot weather versions are required.
Low temperature
Utility-scale wind turbine generators have minimum temperature operating limits which apply in areas that experience temperatures below –20 °C. Wind turbines must be protected from ice accumulation, which can make anemometer readings inaccurate and which can cause high structure loads and damage. Some turbine manufacturers offer low-temperature packages at a few percent extra cost, which include internal heaters, different lubricants, and different alloys for structural elements. If the low-temperature interval is combined with a low-wind condition, the wind turbine will require an external supply of power, equivalent to a few percent of its rated power, for internal heating. For example, the St. Leon, Manitoba project has a total rating of 99 MW and is estimated to need up to 3 MW (around 3% of capacity) of station service power a few days a year for temperatures down to –30 °C. This factor affects the economics of wind turbine operation in cold climates.
Aerodynamics
The aerodynamics of a horizontal-axis wind turbine are not straightforward. The air flow at the blades is not the same as the airflow far away from the turbine. The very nature of the way in which energy is extracted from the air also causes air to be deflected by the turbine. In addition the aerodynamics of a wind turbine at the rotor surface exhibit phenomena that are rarely seen in other aerodynamic fields.
In 1919 the physicist Albert Betz showed that for a hypothetical ideal wind-energy extraction machine, the fundamental laws of conservation of mass and energy allowed no more than 16/27 (59.3%) of the kinetic energy of the wind to be captured. This Betz' law limit can be approached by modern turbine designs which may reach 70 to 80% of this theoretical limit.
Power control
A wind turbine is designed to produce a maximum of power at wide spectrum of wind speeds. All wind turbines are designed for a maximum wind speed, called the survival speed, above which they do not survive. The survival speed of commercial wind turbines is in the range of 40 m/s (144 km/h) to 72 m/s (259 km/h). The most common survival speed is 60 m/s (216 km/h). The wind turbines have three modes of operation:

- Below rated wind speed operation
- Around rated wind speed operation (usually at nameplate capacity)
- Above rated wind speed operation
If the rated wind speed is exceeded the power has to be limited. There are various ways to achieve this.
Stall


Stalling works by increasing the angle at which the relative wind strikes the blades (angle of attack), and it reduces the induced drag (drag associated with lift). Stalling is simple because it can be made to happen passively (it increases automatically when the winds speed up), but it increases the cross-section of the blade face-on to the wind, and thus the ordinary drag. A fully stalled turbine blade, when stopped, has the flat side of the blade facing directly into the wind.
A fixed-speed HAWT inherently increases its angle of attack at higher wind speed as the blades speed up. A natural strategy, then, is to allow the blade to stall when the wind speed increases. This technique was successfully used on many early HAWTs. However, on some of these blade sets, it was observed that the degree of blade pitch tended to increase audible noise levels.
Vortex generators may be used to control the lift characteristics of the blade. The VGs are placed on the airfoil to enhance the lift if they are placed on the lower (flatter) surface or limit the maximum lift if placed on the upper (higher camber) surface.[2]
Pitch control
Furling works by decreasing the angle of attack, which reduces the induced drag from the lift of the rotor, as well as the cross-section. One major problem in designing wind turbines is getting the blades to stall or furl quickly enough should a gust of wind cause sudden acceleration. A fully furled turbine blade, when stopped, has the edge of the blade facing into the wind.
Standard modern turbines all pitch the blades in high winds. Since pitching requires acting against the torque on the blade, it requires some form of pitch angle control, which is achieved with a slewing drive. This drive precisely angles the blade while withstanding high torque loads. In addition, many turbines use hydraulic systems. These systems are usually spring loaded, so that if hydraulic power fails, the blades automatically furl. Other turbines use an electric servomotor for every rotor blade. They have a small battery-reserve in case of an electric-grid breakdown. Small wind turbines (under 50 kW) with variable-pitching generally use systems operated by centrifugal force, either by flyweights or geometric design, and employ no electric or hydraulic controls.
Other controls
Yawing
Modern large wind turbines are typically actively controlled to face the wind direction measured by a wind vane situated on the back of the nacelle. By minimizing the yaw angle (the misalignment between wind and turbine pointing direction), the power output is maximized and non-symmetrical loads minimized. However, since the wind direction varies quickly the turbine will not strictly follow the direction and will have a small yaw angle on average. The power output losses can simply be approximated to fall with cos3(yaw angle).
Electrical braking

Braking of a small wind turbine can also be done by dumping energy from the generator into a resistor bank, converting the kinetic energy of the turbine rotation into heat. This method is useful if the kinetic load on the generator is suddenly reduced or is too small to keep the turbine speed within its allowed limit.
Cyclically braking causes the blades to slow down, which increases the stalling effect, reducing the efficiency of the blades. This way, the turbine's rotation can be kept at a safe speed in faster winds while maintaining (nominal) power output. This method is usually not applied on large grid-connected wind turbines.
Mechanical braking
A mechanical drum brake or disk brake is used to hold the turbine at rest for maintenance. Such brakes are usually applied only after blade furling and electromagnetic braking have reduced the turbine speed, as the mechanical brakes would wear quickly if used to stop the turbine from full speed. There can also be a stick brake.
Turbine size
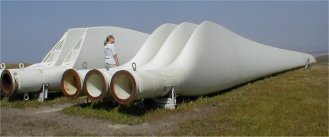
For a given survivable wind speed, the mass of a turbine is approximately proportional to the cube of its blade-length. Wind power intercepted by the turbine is proportional to the square of its blade-length. The maximum blade-length of a turbine is limited by both the strength and stiffness of its material.
Labor and maintenance costs increase only gradually with increasing turbine size, so to minimize costs, wind farm turbines are basically limited by the strength of materials, and siting requirements.
Typical modern wind turbines have diameters of 40 to 90 metres (130 to 300 feet) and are rated between 500 kW and 2 MW. As of 2010 the most powerful turbine is rated at 7 MW.
Generator

For large, commercial size horizontal-axis wind turbines, the generator is mounted in a nacelle at the top of a tower, behind the hub of the turbine rotor. Typically wind turbines generate electricity through asynchronous machines that are directly connected with the electricity grid. Usually the rotational speed of the wind turbine is slower than the equivalent rotation speed of the electrical network - typical rotation speeds for a wind generators are 5-20 rpm while a directly connected machine will have an electrical speed between 750-3600 rpm. Therefore, a gearbox is inserted between the rotor hub and the generator. This also reduces the generator cost and weight.
Commercial size generators have a rotor carrying a field winding so that a rotating magnetic field is produced inside a set of windings called the stator. While the rotating field winding consumes a fraction of a percent of the generator output, adjustment of the field current allows good control over the generator output voltage. Enercon has produced gearless wind turbines with separately excited generators for many years, and Siemens produces a gearless "inverted generator" 3MW model[3][4] while developing a 6MW model.[5] This gives better reliability and performance than gear based systems.[citation needed] Gearless turbines

Older style wind generators rotate at a constant speed, to match power line frequency, which allowed the use of less costly induction generators. Newer wind turbines often turn at whatever speed generates electricity most efficiently. This can be solved using multiple technologies such as doubly fed induction generators or full-effect converters where the variable frequency current produced is converted to DC and then back to AC, matching the line frequency and voltage. Although such alternatives require costly equipment and cause power loss, the turbine can capture a significantly larger fraction of the wind energy. In some cases, especially when turbines are sited offshore, the DC energy will be transmitted from the turbine to a central (onshore) inverter for connection to the grid.
Blades
Blade design
The ratio between the speed of the blade tips and the speed of the wind is called tip speed ratio. High efficiency 3-blade-turbines have tip speed/wind speed ratios of 6 to 7.
Modern wind turbines are designed to spin at varying speeds (a consequence of their generator design, see above). Use of aluminum and composite materials in their blades has contributed to low rotational inertia, which means that newer wind turbines can accelerate quickly if the winds pick up, keeping the tip speed ratio more nearly constant. Operating closer to their optimal tip speed ratio during energetic gusts of wind allows wind turbines to improve energy capture from sudden gusts that are typical in urban settings.
In contrast, older style wind turbines were designed with heavier steel blades, which have higher inertia, and rotated at speeds governed by the AC frequency of the power lines. The high inertia buffered the changes in rotation speed and thus made power output more stable.
The speed and torque at which a wind turbine rotates must be controlled for several reasons:
- To optimize the aerodynamic efficiency of the rotor in light winds.
- To keep the generator within its speed and torque limits.
- To keep the rotor and hub within their centripetal force limits. The centripetal force from the spinning rotors increases as the square of the rotation speed, which makes this structure sensitive to overspeed.
- To keep the rotor and tower within their strength limits. Because the power of the wind increases as the cube of the wind speed, turbines have to be built to survive much higher wind loads (such as gusts of wind) than those from which they can practically generate power. Since the blades generate more downwind force (and thus put far greater stress on the tower) when they are producing torque, most wind turbines have ways of reducing torque in high winds.
- To enable maintenance; because it is dangerous to have people working on a wind turbine while it is active, it is sometimes necessary to bring a turbine to a full stop.
- To reduce noise; As a rule of thumb, the noise from a wind turbine increases with the fifth power of the relative wind speed (as seen from the moving tip of the blades). In noise-sensitive environments, the tip speed can be limited to approximately 60 m/s (200 ft/s).
Blade count

The determination of the number of blades involves design considerations of aerodynamic efficiency, component costs, system reliability, and aesthetics. Noise emissions are affected by the location of the blades upwind or downwind of the tower and the speed of the rotor. Given that the noise emissions from the blades' trailing edges and tips vary by the 5th power of blade speed, a small increase in tip speed can make a large difference.
Wind turbines developed over the last 50 years have almost universally used either two or three blades. Aerodynamic efficiency increases with number of blades but with diminishing return. Increasing the number of blades from one to two yields a six percent increase in aerodynamic efficiency, whereas increasing the blade count from two to three yields only an additional three percent in efficiency. Further increasing the blade count yields minimal improvements in aerodynamic efficiency and sacrifices too much in blade stiffness as the blades become thinner.
Component costs that are affected by blade count are primarily for materials and manufacturing of the turbine rotor and drive train. Generally, the fewer the number of blades, the lower the material and manufacturing costs will be. In addition, the fewer the number of blades, the higher the rotational speed can be. This is because blade stiffness requirements to avoid interference with the tower limit how thin the blades can be manufactured, but only for upwind machines; deflection of blades in a downwind machine results in increased tower clearance. Fewer blades with higher rotational speeds reduce peak torques in the drive train, resulting in lower gearbox and generator costs.

System reliability is affected by blade count primarily through the dynamic loading of the rotor into the drive train and tower systems. While aligning the wind turbine to changes in wind direction (yawing), each blade experiences a cyclic load at its root end depending on blade position. This is true of one, two, three blades or more. However, these cyclic loads when combined together at the drive train shaft are symmetrically balanced for three blades, yielding smoother operation during turbine yaw. Turbines with one or two blades can use a pivoting teetered hub to also nearly eliminate the cyclic loads into the drive shaft and system during yawing.
Finally, aesthetics can be considered a factor in that some people find that the three-bladed rotor is more pleasing to look at than a one- or two-bladed rotor.
Blade materials
New generation wind turbine designs are pushing power generation from the single megawatt range to upwards of 10 megawatts. The common trend of these larger capacity designs are larger and larger wind turbine blades. Covering a larger area effectively increases the tip-speed ratio of a turbine at a given wind speed, thus increasing the energy extraction capability of a turbine system.[6]
Current production wind turbine blades are manufactured as large as 100 meters in diameter with prototypes in the range of 110 to 120 meters. In 2001, an estimated 50 million kilograms of fiberglass laminate were used in wind turbine blades.[7] New materials and manufacturing methods provide the opportunity to improve wind turbine efficiency by allowing for larger, stronger blades.
One of the most important goals when designing larger blade systems is to keep blade weight under control. Since blade mass scales as the cube of the turbine radius, loading due to gravity becomes a constraining design factor for systems with larger blades.[8]
Current manufacturing methods for blades in the 40 to 50 meter range involve various proven fiberglass composite fabrication techniques. Manufactures such as Nordex and GE Wind use an infusion process for blade manufacture. Other manufacturers use variations on this technique, some including carbon and wood with fiberglass in an epoxy matrix. Options also include prepreg fiberglass and vacuum-assisted resin transfer molding. Essentially each of these options are variations on the same theme: a glass-fiber reinforced polymer composite constructed through various means with differing complexity. Perhaps the largest issue with more simplistic, open-mold, wet systems are the emissions associated with the volatile organics released into the atmosphere. Preimpregnated materials and resin infusion techniques avoid the release of volatiles by containing all reaction gases. However, these contained processes have their own challenges, namely the production of thick laminates necessary for structural components becomes more difficult. As the preform resin permeability dictates the maximum laminate thickness, bleeding is required to eliminate voids and insure proper resin distribution.[7] A unique solution to resin distribution is the use of a partially preimpregnated fiberglass. During evacuation, the dry fabric provides a path for airflow and, once heat and pressure are applied, resin may flow into the dry region resulting in a thoroughly impregnated laminate structure.[7]
Epoxy-based composites are of greatest interest to wind turbine manufacturers because they deliver a key combination of environmental, production, and cost advantages over other resin systems. Epoxies also improve wind turbine blade composite manufacture by allowing for shorter cure cycles, increased durability, and improved surface finish. Prepreg operations further improve cost-effective operations by reducing processing cycles, and therefore manufacturing time, over wet lay-up systems. As turbine blades are approaching 60 meters and greater, infusion techniques are becoming more prevalent as the traditional resin transfer moulding injection time is too long as compared to the resin set-up time, thus limiting laminate thickness. Injection forces resin through a thicker ply stack, thus depositing the resin where in the laminate structure before gelatin occurs. Specialized epoxy resins have been developed to customize lifetimes and viscosity to tune resin performance in injection applications.[9]
Carbon fiber-reinforced load-bearing spars have recently been identified as a cost-effective means for reducing weight and increasing stiffness. The use of carbon fibers in 60 meter turbine blades is estimated to result in a 38% reduction in total blade mass and a 14% decrease in cost as compared to a 100% fiberglass design. The use of carbon fibers has the added benefit of reducing the thickness of fiberglass laminate sections, further addressing the problems associated with resin wetting of thick lay-up sections. Wind turbine applications of carbon fiber may also benefit from the general trend of increasing use and decreasing cost of carbon fiber materials.[7]
Smaller blades can be made from light metals such as aluminum. Wood and canvas sails were originally used on early windmills due to their low price, availability, and ease of manufacture. These materials, however, require frequent maintenance during their lifetime. Also, wood and canvas have a relatively high drag (low aerodynamic efficiency) as compared to the force they capture. For these reasons they have been mostly replaced by solid airfoils.
Tower
Typically, 2 types of towers exist: floating towers and land-based towers.
Tower height
Wind velocities increase at higher altitudes due to surface aerodynamic drag (by land or water surfaces) and the viscosity of the air. The variation in velocity with altitude, called wind shear, is most dramatic near the surface.
Typically, in daytime the variation follows the wind profile power law, which predicts that wind speed rises proportionally to the seventh root of altitude. Doubling the altitude of a turbine, then, increases the expected wind speeds by 10% and the expected power by 34%. To avoid buckling, doubling the tower height generally requires doubling the diameter of the tower as well, increasing the amount of material by a factor of at least four.
At night time, or when the atmosphere becomes stable, wind speed close to the ground usually subsides whereas at turbine hub altitude it does not decrease that much or may even increase. As a result the wind speed is higher and a turbine will produce more power than expected from the 1/7th power law: doubling the altitude may increase wind speed by 20% to 60%. A stable atmosphere is caused by radiative cooling of the surface and is common in a temperate climate: it usually occurs when there is a (partly) clear sky at night. When the (high altitude) wind is strong (a 10-meter (33 ft) wind speed higher than approximately 6 to 7 m/s (20–23 ft/s)) the stable atmosphere is disrupted because of friction turbulence and the atmosphere will turn neutral. A daytime atmosphere is either neutral (no net radiation; usually with strong winds and/or heavy clouding) or unstable (rising air because of ground heating — by the sun). Here again the 1/7th power law applies or is at least a good approximation of the wind profile. Indiana had been rated as having a wind capacity of 30,000 MW, but by raising the expected turbine height from 50 m to 70 m, the wind capacity estimate was raised to 40,000 MW, and could be double that at 100 m.[10]
For HAWTs, tower heights approximately two to three times the blade length have been found to balance material costs of the tower against better utilisation of the more expensive active components.
Foundations
Wind turbines, by their nature, are very tall slender structures,[11] this can cause a number of issues when the structural design of the foundations are considered.
The foundations for a conventional engineering structure are designed mainly to transfer the vertical load (dead weight) to the ground, this generally allows for a comparatively unsophisticated arrangement to be used. However in the case of wind turbines, due to the high wind and environmental loads experienced there is a significant horizontal load that needs to be accounted for.
This loading regime causes large moment loads to be applied to the foundations of a wind turbine. As a result, considerable attention needs to be given when designing the footings to ensure that the turbines are sufficiently restrained to operate efficiently.[12] In the current Det Norske Veritas (DNV) guidelines for the design of wind turbines the angular deflection of the foundations are limited to 0.5°.[13]
Scale model tests using a 50g centrifuge are being performed at the Technical University of Denmark to test monopile foundations for offshore wind turbines at 30-50m water depth.[14]
See also
- Brushless wound-rotor doubly-fed electric machine
- Vertical-axis wind turbine
- Wind turbine
- Wind turbine aerodynamics
- Wind farm
References
- ^ a b "Efficiency and performance" (PDF). UK Department for Business, Enterprise & Regulatory Reform. Retrieved 2007-12-29.
- ^ Johnson, Scott J. (2008). "Active Load Control Techniques for Wind Turbines" (PDF). Sandia National Laboratory. Retrieved 13 September 2009.
{{cite web}}
: Unknown parameter|coauthors=
ignored (|author=
suggested) (help) - ^ Fairly, Peter. Wind Turbines Shed Their Gears Technology Review, 27 April 2010. Retrieved: 22 September 2010.
- ^ Wittrup, Sanne. First Siemens gearless Ing.dk, 11 August 2010. Retrieved: 15 September 2010.
- ^ Wittrup, Sanne. 6MW Siemens gearless Ing.dk, 15 September 2010. Retrieved: 15 September 2010.
- ^ Zbigniew Lubosny (2003). Wind Turbine Operation in Electric Power Systems: Advanced Modeling (Power Systems). Berlin: Springer. ISBN 3-540-40340-X.
- ^ a b c d Griffin, Dayton A.; Ashwill, Thomas D. (2003). "Alternative Composite Materials for Megawatt-Scale Wind Turbine Blades: Design Considerations and Recommended Testing". Journal of Solar Energy Engineering. 125: 515. doi:10.1115/1.1629750.
- ^ Ashwill, T (2007). Concepts to Facilitate Very Large Blades (PDF). 45th AIAA Aerospace Sciences Meeting and Exhibit. AIAA-2007-0817.
{{cite conference}}
: Unknown parameter|coauthors=
ignored (|author=
suggested) (help); Unknown parameter|month=
ignored (help) - ^ Christou, P (2007). "Advanced materials for turbine blade manufacture". Reinforced Plastics. 51: 22. doi:10.1016/S0034-3617(07)70148-0.
- ^ Indiana's Renewable Energy Resources
- ^ Lombardi, D. (2010). Long Term Performance of Mono-pile Supported Offshore Wind Turbines. Bristol: University of Bristol.
- ^ Cox, J. A., & Jones, C. gggggggggggggggggggggggggggggggggggg(2010). Long-Term Performance of Suction Caisson Supported Offshore Wind Turbines. Bristol: University of Bristol.
- ^ Det Norske Veritas (2001). Guidelines for Design of Wind Turbines. Copenhagen: Det Norske Veritas.
- ^ Rasmussen, Daniel. Wind turbine foundations at 50g (in Danish) Ing.dk, 26 October 2010. 6minute Video Retrieved: 25 November 2010.
This article needs additional citations for verification. (July 2008) |