Oil shale
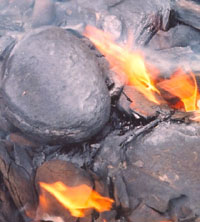
Oil shale is a general term applied to a fine-grained sedimentary rock containing significant traces of kerogen (a solid mixture of organic chemical compounds) that have not been buried for sufficient time to produce conventional fossil fuels. When heated to a sufficiently high temperature a vapor is driven off which can be distilled (retorted) to yield a petroleum-like shale oil—a form of non-conventional oil—and combustible shale gas.
The kerogen in oil shale can be converted to oil through the chemical process of pyrolysis. Oil shale can also be burnt directly as a low-grade fuel for power generation and heating, and be used as a raw material in the chemical and construction materials industries. Currently oil shales are used commercially for oil production in Estonia, Brazil and China, for power generation in Estonia, China, Israel and Germany, for cement production in Estonia, Germany and China, and for chemical industry in Estonia and Russia.[1][2][3]
World deposits of oil shale are estimated to equal 2.9–3.3 trillion barrels of recoverable oil, 1.5–2.6 trillion barrels of which are in the United States.[4][5][6][7] Attempts to develop these reserves, ongoing for over 150 years, have had limited success.[8] Although still seen as a potential future alternative to conventional oil, world production reached a peak of 46 million tons in 1980 before falling to about 16 million tons in 2000 due to the high cost of production relative to conventional petroleum.[9][10]
Environmentalists have expressed concern over the extraction of shale oil,[10] and protests appear to have contributed to the halting of the developing industry in Australia. [11]
In addition to the oil shale, there are other groups of organic-rich sedimentary rock—bitumen-impregnated rocks (tar sands and petroleum reservoir rocks), and humic coals and carbonaceous shale.[12]
Geology
Classification and varieties
Oil shale does not have a specific chemical formula. Different types of oil shales vary in their chemical composition, type of kerogen, age, and depositional history, including the organisms from which they were derived.[13]
Oil shales have been divided into three categories depending on their composition. These three categories are carbonate-rich shale, siliceous shale and cannel shale. Carbonate-rich shales derive their name from the large amount of carbonate minerals such as calcite and dolomite that can be found in it. As many as 20 carbonate minerals have been found in oil shale, the majority of which have thought to have been deposited at the time of deposition. One type of carbonate-rich shale that is valued quite highly is lacustrine-sourced deposits, because of the frequent occurrence of organic-rich shale layers sandwiched between carbonate-rich layers of oil shale. These deposits are hard formations which could be difficult to process using ex-situ methods.[14] Siliceous shales derive their names as they are not rich in carbonate deposits but rather Detritus detrital minerals. Detrital minerals that have been known to be present are quartz, feldspar, clay, chert and opal. Younger siliceous shales can be good sources for hydrocarbons, but as the deposits get older and deeper the hydrocarbons that might have been present have generally migrated. Siliceous shales are not as hard or as weather-resistant as carbonate-rich shale and may be better suited for extraction via ex-situ methods.[14]
Based upon environment of deposition, oil shales are characterized as terrestrial, lacustrine, and marine.
Terrestrial | Lacustrine | Marine |
---|---|---|
cannel coal | lamosite; torbanite | kukersite; tasmanite; marinite |
Cannel coal is brown to black coal (sometimes with shaly texture) composed of resins, spores, waxes, cutinaceous and corky materials derived from terrestrial vascular plants as well as varied amounts of vitrinite and inertinite. Lamosite is pale brown and grayish-brown to dark-gray to black oil shale in which the chief organic constituent is lamalginite derived from lacustrine planktonic algae. Marinite is a gray to dark-gray to black oil shale of marine origin in which the chief organic components are lamalginite and bituminite derived from marine phytoplankton with varied admixtures of bitumen, telalginite, and vitrinite. Torbanite, named after Torbane Hill in Scotland, is a black oil shale whose organic matter is telalginite derived from lipid-rich Botryococcus and related algal forms. Tasmanite, named after Tasmania, is a brown to black oil shale whose organic matter consists of telalginite derived chiefly from unicellular tasmanitid algae of marine origin. Kukersite, named after Kukruse in Estonia, is a light-brown marine oil shale whose principal organic component is telalginite derived from the green alga, Gloeocapsomorpha prisca.[16]
Composition
Organic matter in oil shale consists of the remains of algae, spores, pollen, plant cuticles and corky fragments of herbaceous and woody plants, and cellular debris from other lacustrine, marine, and land plants. While terrestrial oil shales contains resins, spores, waxy cuticles, and corky tissue of roots and stems of vascular terrestrial plants, lacustrine oil shales include lipid-rich organic matter derived from algae, and marine oil shales are composed of marine algae, acritarchs, and marine dinoflagellates. Some oil-shale deposits may also contain non-organic minerals and metals including alum, nahcolite (NaHCO3), dawsonite, sulfur, ammonium sulfate, vanadium, zinc, copper, uranium, and others.[16]
Country | Location | Type | Age | Organic carbon (%) | Oil yield (%) | Oil conversion ratio (%) |
---|---|---|---|---|---|---|
Australia | Glen Davis, New South Wales | torbanite | Permian | 40 | 31 | 66 |
Tasmania | tasmanite | Permian | 81 | 75 | 78 | |
Brazil | Irati | marinite | Permian | 7.4 | ||
Paraíba Valley | lacustrine shales | Permian | 13-16.5 | 6.8-11.5 | 45-59 | |
Canada | Nova Scotia | torbanite; lamosite | Permian | 8-26 | 3.6-19 | 40-60 |
China | Fushun | cannel coal; lacustrine shales | Eocene | 7.9 | 3 | 33 |
Estonia | Estonia Deposit | kukersite | Ordovician | 77 | 22 | 66 |
France | Autun, St. Hilarie | Permian | 8-22 | 5-10 | 45-55 | |
Creveney, Severac | Toarcian | 5-10 | 4-5 | 60 | ||
South Africa | Ermelo | Permian | 44-52 | 18-35 | 34-60 | |
Spain | Puertollano | lacustrine shale | Permian | 26 | 18 | 57 |
Sweden | Kvarntorp | marinite | Lower Paleozic | 19 | 6 | 26 |
United Kingdom | Scotland | torbanite | 12 | 8 | 56 | |
United States | Alaska | Jurassic | 25-55 | 0.4-0.5 | 28-57 | |
Green River Formation in Colorado, Wyoming and Utah | lamosite | Eocene | 11-16 | 9-13 | 70 | |
Mississippi | marinite | Devonian |
Formation
Oil shale is considered to be formed by the deposition of organic matter in lakes, lagoons and restricted estuarine areas such as oxbow lakes, peat bogs, swamps, and muskegs. When plants die in such anaerobic aquatic environments, low oxygen levels prevent their complete decay by bacteria.[citation needed] For masses of undecayed organic matter to be preserved and to form oil shale the environment must remain uniform for prolonged periods of time to build up sufficiently thick sequences of algal matter. Unlike coal, oil shale does not necessarily require low mineral and ash content, as it is used mainly for extraction, and mineral waste in oil liquefaction plants is easier to deal with.[citation needed]
Eventually the algal swamp or other restricted environments are disrupted and oil shale accumulation ceases. Burial by sedimentary loading on top of the algal swamp deposits converts the organic matter to kerogen by the following normal diagenetic processes[citation needed]:
- Compaction due to loading of the sediments on the coal which compresses the organic matter
- Removal of the water in the peat
- With ongoing compaction, removal of water from the intracellular structure of fossilized plants
- With heat and compaction, removal of molecular water
- Methanogenesis; similar to treating wood in a pressure cooker, methane is produced, removing hydrogen, some carbon, and some further oxygen (as water)
- Dehydration, which removes hydroxyl groups from the cellulose and other plant molecules, resulting in the production of hydrogen-reduced coals
Lower temperature and pressure during the diagenesis process compared to other modes of hydrocarbon genesis result in the achievement of a lower maturation level shown by oil shale reserves. Continued burial and further applied heating and pressure combined with the correct geological structures could result in the production of oil and gas reservoir from the oil shale source rock.[17] The largest deposits are found in the remains of large lakes like those deposits at Green River, other deposits can in shallow sea’s that were on continentals shelf's and smaller shale deposits can be found in lagoons and lakes similar depositional environments to where coal is formed.[citation needed] Large lake oil shale basins can be found where there has been block faulting or crustal warping due to mountain building. As a some of the larger deposits known can be found in these regions like along the Rocky Mountains where the majority of Americas oil shale's are located. Deposits such as the Green River can be as much as 600 m (2000 ft) and yield up to 40 gallons of oil for each ton (166 L/t) of shale.[citation needed]
Shale's formed in the shallow seas of continental shelves generally are much thinner than large lake basin deposits generally in the order of feet or tens of feet thick. They are however due to the depositional nature spread over a very large surface area stretching up to thousands of square kilometres. Of the three lithologic types of shales, siliceous shales are the most commonly found in this environment. These shales are not as energy rich as the previous shales and generally do not contain more than 30 gallons per ton (125 L/t) of shale.[citation needed] Oil shales deposited in lagoonal or small lake environments are rarely extensive and are often associated with coal bearing rocks. These shales though can have high yields close to 40 gallons per ton (166 L/t) of shale however due to their sporadic placement and thin bed nature they are thought to be unlikely candidates for commercial exploitation. Most shales are of the cannel type.[citation needed]
Formations in the United States
The United States has two significant oil-shale deposits which are considered suitable for development due to their size, grade, location and the understanding of them. These two deposits are the Eocene Green River Formation which covers parts of Colorado, Wyoming and Utah, and Devonian deposits in the eastern United States. In both of these plays there are sub-basins in which the volume and quality of the reserves vary. Oil shale in the Green River Formation is found in five sedimentary basins: Green River, Uinta, Piceance Creek, Sand Wash and Washakie. The first three have undergone some significant investigation and attempts to commercialise the oil shale reserves since the 1960’s. The Green River Formation includes deposits from two large lakes which covered an area of over 65,000 square kilometers during the early to middle Eocene period. These lakes were separated by the Uinta uplift and the Axial Basin anticline.[citation needed] For significant periods during their 10-million-year life, the lakes became closed systems allowing for many changes in size, salinity and sediment deposition. Oil shale is a result of abundant blue-green algae that thrived in the lakes during such times.[citation needed]
The oil shale that underlies almost three quarters of a million square kilometers in the eastern United States was formed in a marine depositional environment very different from the Green River Basins. These deposits have also undergone commercialisation attempts; they are also resources for natural gas and have been mined for low-grade oil shale. These oil shales were formed during the Late Devonian and Early Mississippian periods. During this time much of the eastern United States was covered by a large shallow sea. The oil shale is thought to have been the result of slow deposition of planktonic algae under quiet conditions. In parts close to the shoreline the organic mixture that helped form the oil shale contains organic-rich sediment from the rising Appalachian mountains.[citation needed]
Brazilian oil shale formations
Brazil has nine significant oil shale deposits. The size, location and quality of shale oil deposits in the Paraiba Valley and the Irati Formation have attraced the most attention. The two contain an estimated 1.4 billion barrels of in-situ shale oil with total resources as much as 3 or more billion barrels. While the Irati Formation play is the smaller of the two, containing an estimated 600 million barrels in-situ compared to 840 million in the Paraiba Valley formation, it is the more economically viable.[citation needed]
The Irati Formation consists of two beds of oil shale separated by 12 m of limestone and shale. The upper layer is thicker (approximately 9 m) but the thinner lower bed (4 m) is of greater value; the weight percent of shale oil yield is around 12% compared to 7%. This oil shale yield varies depending on location, and may be as little as 7% for the lower and 4% for the upper layer. The formation is a very fine grained and laminated deposit ranging in colour from dark grey to brown to black. 60-70% of the shale is clay minerals; organic matter makes up the rest.[citation needed] No definitive consensus has been reached on the exact depositional nature of the shale. The two leading theories are that the organic material is from an algae deposited in a freshwater to brackish lacustrine environment. Alternatively, the organic sediment may have been deposited in a shallow, partially restricted marine basin. Hutton[citation needed] has described it as a marine source shale.
Reserves
The world deposits of oil shale are estimated to be equal to 2.9-3.3 trillion barrels of recoverable oil. Although oil shale resources occur in many countries, only 33 countries possess deposits of economic value.[9] Total resources of these countries are estimated at 411 billion tonnes, which is equal to 2.9 trillion U.S. barrels.[16] Among those, USA accounts for 62% of the world resources, and USA, Russia and Brazil together account for 86% in terms of shale oil content.[9] The above mentioned figure of total reserves is conservative because several deposits have not been explored sufficiently to make accurate estimates, and other deposits were not included.[16][18]
Estimating shale oil reserves is complicated by several factors. First, the amount of kerogen contained in oil shale deposits varies considerably. Second, some nations report as reserves the total amount of kerogen in place, which means all kerogen regardless of technical or economic constraints, and not as an estimate of kerogen which may be extracted from identified and assayed oil shale rock using available technology and under current economic conditions. Third, by definition, "reserves" refers only to the amount of resource which is technically exploitable and economically feasible under current economic conditions. Fourth, shale oil recovery technologies are still developing, so the amount of recoverable kerogen can only be estimated.[citation needed]
The table below reports reserves by amount of shale oil. Shale oil refers to synthetic oil obtained by heating organic material (kerogen) contained in oil shale rock to a temperature which will convert it to oil, combustible gas, and residual carbon that remains in the spent shale. All figures are presented in barrels and metric tons ("tonnes", equal to 2204.6 pounds).[19]
Region | In-place shale oil resources (million barrels) | In-place oil shale resources (million tonnes) | Production in 2002(thousand tonnes (oil)) |
---|---|---|---|
Africa | 159,243 | 23,317 | - |
Asia | 45,894 | 6,562 | 100 |
Europe | 368,156 | 52,845 | 275 |
Middle East | 38,172 | 5,792 | - |
North America | 2,602,469 | 382,758 | - |
Oceania | 31,748 | 4,534 | 46 |
South America | 82,421 | 11,794 | 157 |
Africa
Major oil shale deposits are located in the Democratic Republic of Congo (equal to 14.31 billion tonnes of shale oil) and Morocco (12.3 billion tonnes or 8.16 billion tonnes of shale oil). The biggest deposits in Morocco are Tarfaya and Timahdit. There are oil shale reserves also in Egypt, South Africa, Madagascar and Nigeria.[16]
Asia
Major oil shale deposits are located in China (total, 32 billion tonnes of which technically exploitable and economically feasible is 4.4 billion tonnes), Thailand (18.7 billion tonnes), Kazakhstan (several deposits; major deposit at Kenderlyk Field with 4 billion tonnes) and Turkey (2.2 billion tonnes).[16][13][20] There are oil shale reserves also in Uzbekistan, Turkmenistan, Myanmar, Armenia and Mongolia. The main Chinese oil shale deposits and production lie in Fushun and Liaoning; others are in Maoming in Guangdong, Huadian in Jilin, Heilongjiang and Shandong. In 2002, China produced more than 90,000 tonnes of shale oil.[20] Thailand's oil shale deposits are near Mae Sot, Tak Province, and at Li, Lamphun Province. Deposits in Turkey are located mainly in middle and western Anatolia.[16]
Europe
The biggest oil shale reserves in Europe are located in Russia (equal to 35.47 billion tonnes of shale oil). Main deposits are located in the Volga-Petchyorsk province and the Baltic Basin. Other major oil shale deposits in Europe are located in Italy (10.45 billion tonnes of shale oil), Estonia (2.49 billion tonnes of shale oil), France (1 billion tonnes of shale oil), Belarus (1 billion tonnes of shale oil), Sweden (875 million tonnes of shale oil), Ukraine (600 million tonnes of shale oil) and the United Kingdom (500 million tonnes of shale oil). There are oil shale reserves also in Germany, Luxembourg, Spain, Bulgaria, Hungary, Poland, Austria, Albania and Romania.[16]
Middle East
Major oil shale deposits are located in Jordan (5,242 million tonnes of shale oil or 65 billion tonnes of oil shale) and Israel (550 million tonnes of shale oil or 6.5 billion tonnes of oil shale). Jordanian oil shales are high quality, comparable to western US oil shale, with the exception of high sulfur content. The most explored deposits are El Lajjun, Sultani and the Juref ed Darawishare located in west-central Jordan, while Yarmouk close to the northern border extends into Syria.[16][21] Most of Israel's deposits are located in the Rotem Basin region of the northern Negev desert near the Dead Sea. Israeli oil shale is relatively low in heating value and oil yield.[16][22]
North America
At 3.3 trillion tonnes, the oil shale deposits in the United States are easily the largest in the world. There are two major deposits: the eastern US deposits, in Devonian-Mississippian shales, cover 250,000 square miles (650,000 square kilometers); the western US deposits of the Green River Formation in Colorado, Wyoming and Utah, are among the richest oil shale deposits in the world.[16][23] In Canada 19 deposits have been identified. The most explored deposits are in Nova Scotia and New Brunswick.[24]
Oceania
Australia's oil shale resource is estimated to be around 58 billion tonnes or 4,531 million tonnes of shale oil. The deposits are located in the eastern and southern states with the biggest potential in the eastern Queensland deposits.[16] There is also oil shale in New Zealand.[25]
South America
Brazil has the world's second largest known oil shale resources (the Irati shale and lacustrine deposits) and has the second largest shale oil production after Estonia. Oil shale resources occur in São Mateus do Sul, Paraná, and in Vale do Paraíba. Brazil developed the world’s largest surface oil shale pyrolysis retort Petrosix, an 11-m vertical shaft retort. Production in 1999 was about 200,000 tonnes.[26][13] Small resources are also found in Argentina, Chile, Paraguay, Peru, Uruguay and Venezuela.[27]
Industry
Currently oil shale is used industrially in Brazil, China, Estonia and to some extent in Germany, Israel and Russia, while several other countries research their reserves, have experimental production or have phase-out their oil shale industry.[28] Estonia accounts for about 70% of the world's oil shale production.[29]
History of usage
Oil shale has been used since ancient times. In 1637, Swedish alum shale of Cambrian and Ordovician age was used for extracting potassium aluminium sulfate.[28] The modern use of oil shale for shale oil production dates to the mid-19th century. In 1837 oil shale mining began at the Autun mines in France, and continued until 1957.[26] In 1847 the Scottish chemist James Young prepared "lighting oil," lubricating oil and wax from torbanite. In 1850 he patented the process of cracking oil.[30] Oil from oil shale was produced in Scotland from 1857 until 1962 when production ceased due to the lower cost of petroleum.[28] Germany developed its shale oil industry from mid-19th century until the 1940s. Today, only Rohrbach Zement in Dotternhausen uses oil shale for cement, and power and thermal energy production.[28] Sweden retorted oil from shale from the end of the 19th century until 1966. In addition, in 1950-1989 alum shale was used in Sweden for uranium production and in the 1960s a small amount of vanadium was produced.[16][28]
Estonia first used oil shale as a low-grade fuel in 1838 after attempts to distill oil from the material failed. Estonia's resource was not seriously exploited until fuel shortages during World War I made it viable. Mining began in 1918 and has continued since, with the size of operation increasing with demand. After World War II, Estonian-produced oil shale gas was used in Leningrad and the cities in North Estonia as a substitute for natural gas.[31][32] Two large oil shale-fired power stations were opened, a 1,400-MW plant in 1965 and a 1,600-MW plant in 1973. Oil shale production peaked in 1980 at 31.35 million tonnes. However, in 1981 the fourth reactor of the Sosnovy Bor nuclear power station opened nearby in Leningrad Oblast of Russia, reducing demand for Estonian shale. Production gradually decreased until 1995, since which time production has increased again slightly.[28]
Australia mined 4 million tonnes of oil shale between 1862 and 1952, when government support of mining ceased. Since the 1970s, oil companies have been exploring again possible reserves.[28] From 2000 to 2004 a demonstration-scale processing plant at the Stuart Deposit near Gladstone, Queensland produced over 1.5 million barrels of oil. The facility is now on care-and-maintenance in an operable condition, and the operator of the plant — Queensland Energy Resources — is conducting research and design studies for the next phase of its oil shale operations.[33] Brazil has produced oil from oil shales since 1935. Since 1954 Oil shale development has been the focus of a specific department with in Petrobras named, Superintendencia da Industrializaco do Xisto (SIX). Initially SIX focused on oil shales in the larger Paraíba formation but has now since since refocued development in the Irati shale. The pilot plant with a prototype oil-shale retort was started in 1972 before using Petrosix technology in 1982 and the commercial production started in 1992.[28] China has been mining oil shale since the 1920s near Fushun and Maoming.[3][28] Russia has been mining its reserves since the 1930s. As most of Russian oil shale mines were closed on 1990s, the current production continues on a small-scale basis.[28] Canada has produced some shale oil in mid of 1800s and in 1929-1930. Some experimental processing took place also in 1988.[28]
The United States has seen some attempts at large-scale exploitation. Oil distilled from shale was first burnt for horticultural purposes in the 19th century, but it was not until the 1900s that larger investigations were made. The Office of Naval Petroleum and Oil Shale Reserves was established in 1912. The reserves were seen as a possible emergency source of fuel for the military, particularly the Navy.[citation needed] After World War II, the US Bureau of Mines opened a demonstration mine at Anvils Point, just west of Rifle, Colorado, which operated at a small-scale.[citation needed] In the early sixties TOSCO (The Oil Shale Corporation) opened an underground mine and built an experimental plant near Parachute, Colorado. It closed in the late sixties because the price of production exceeded the cost of imported crude oil.[citation needed] It was not until the oil crisis of the 1970s and the US becoming a net importer of oil that efforts at utilization were increased. Military uses were deemed less important and commercial exploitation came to the fore, with several oil companies investing. Unocal returned to the same area where TOSCO had worked. Several billion dollars were spent until declining oil prices rendered production uneconomical once more and Unocal withdrew in 1991.[citation needed] The oil shale development program was initiated in 2003 in support of President Bush’s National Energy Policy.[34] The Energy Policy Act of 2005 introduced a commercial leasing program for oil shale and tar sands resources on public lands with an emphasis on the most geologically prospective lands within each of the states of Colorado, Utah, and Wyoming.[35] The federal government currently owns 72% of all known oil shale in the United States.
Mining
The oil shale is mined either by traditional underground mining or surface mining techniques. There are several mining methods, but the aim of all of them is the fragmenting of oil shale deposit to enable the transport of shale fragments to a power plant or retorting facility. Main methods of surface mining are open pit mining and strip mining. The main sub-surface mining method is the room-and-pillar method.[36]
Power generation
Oil shale could be used as a fuel for thermal power plants, where the shale is burned like coal to drive steam turbines. Currently there are oil shale-fired power plants in Estonia (2967 MW installed capacities), Israel (12.5 MW), Germany (9.9 MW), and China.[9][20] While some countries have closed their oil shale-fired power plants (e.g. Romania) or converted to other fuels (e.g. Russia), some other countries are looking for construction of these power plants (e.g. Jordan and Egypt), or burn oil shale at the power plants together with coal (e.g. Canada and Turkey).[9][21][37]
There are three technologies for combustion:[2]
- Pulverized Combustion (PC) - used in the older units of oil shale-fired power plants in Estonia
- Fluidized Bed Combustion (FBC) - used by Rohrbach Zement in Dotternhausen, Germany
- Circulated Fluidized Bed (CFB) - used in two new units at Narva Power Plants in Estonia, Huadian Power Plant in China, and PAMA power plant at Mishor Rotem in Israel.
The most modern technology of a combustion of oil shale in power plants is a bubbling fluidized bed (BFB) or circulating fluidized bed (CFB) process, while the traditional way of burning oil shale is through pulverized combustion.[38][9]
Oil extraction
At present, the major shale oil producers are Estonia, Brazil and China, while some other countries as Australia, USA, Canada and Jordan have planned to start or restart shale oil production.[9][21] Although there are several oil shale retorting technologies, only five technologies are currently in commercial use, which are Kiviter, Galoter, Fushun, Petrosix, and Alberta Taciuk.[39]
The two main methods of extracting oil from shale are ex-situ and in-situ.
Heating Method | Above Ground (ex-situ) | Below Ground (in-situ) |
---|---|---|
Conduction through a wall (various fuels) | Pumpherston, Fischer assay, Oil-Tech | Shell ICP (primary method) |
Externally generated hot gas | PetroSIX, Union B, Paraho Indirect, Superior Indirect | - |
Internal combustion | Kiviter, Fushun, Union A, Paraho Direct, Superior Direct | Oxy MIS, LLNL RISE, Geokinetics Horizontal, Rio Blanco |
Hot recycled solids (inert or burned shale) | Alberta Taciuk, Galoter, Lurgi, TOSCO II, Chevron STB, LLNL HRS, Shell Spher | - |
Reactive fluids | IGT Hytort (high-pressure H2), Donor solvent processes | Shell ICP (some embodiments) |
Volumetric heating | - | ITTRI and LLNL radiofrequency |
Ex-situ
In case of the ex-situ method, the oil shale is/can be mined either by traditional underground mining or surface mining from the ground and then transported to a processing facility. At the facility, the shale is usually heated to 450–500 °C (750-950°F). At this temperature, the kerogen in the shale decomposes to gas, oil vapour and char, a process known as retorting. The gas and oil vapours are separated from the spent shale and cooled causing the oil to condense. The oil may be sold as a fuel oil or upgraded to meet refinery feed specifications by adding hydrogen and removing impurities such as sulphur and nitrogen. The non-condensible retort gas and char on the spent shale may be burned and the heat may be recovered for heating the raw shale or generating electricity. Combustion exhaust gases and water condenced with the oil need to be treated prior to emission to the environment. Usually the spent shale is cooled and moistened with water before disposal back to the mine, settling ponds or tailing piles.
There are hundreds of patents for oil shale retorting technologies. However, only a few dozen have been tested in a pilot plant (1 to 10 t/h) and less than 10 technologies have been tested at a demonstration scale (40 to 400 t/h). One method of classifying the different ex-situ technologies is by the method that is used to heat the shale to retorting temperature. The classes are internal combustion technologies, hot recycled solids technologies, conduction through a wall technologies, externally generated hot gas technologies, and reactive fluids technologies.[40]
Internal combustion technologies
Internal combustion or directly heated technologies uses heat, which is transferred by flowing gases generated by combustion within the retort. Common characteristics of these technolgies are the feed shale consists of lumps (10-100 mm) and the retort vapours are diluted with the combustion exhaust. The main technologies are Kiviter, Union A, Paraho Direct, Superior Direct, and Fushun processes.[40][41] The Kiviter processing takes place in gravitational shaft retorts and it's possible only using large-particle feed. The process gas combustion products are used as the heat carrier. In the case of kukersite the yield of crude oil accounts 14-17% of shale and the oil consists only small amount of low-boiling fractions. Main problems of Kiviter process are related with environmental concerns like extensive use and pollution of water in the process, as also solid residue continues to leach toxic substances.[42][43] The Kiviter process is used by Estonian company VKG Oil, a subsidiary of Viru Keemia Grupp.[44] The company operates several retorts, the largest processing 40 t/h of oil shale.
Like the Kiviter, the Fushun-type retort processes oil shale lumps in a vertical shaft kiln. The Fushun Mining Group in Liaoning Province, China operates the largest shale oil plant in the world employing 80 Fushun-type retorts.[45] The Paraho Direct is an American version of the lump-processing vertical shaft kiln. Shale Technologies LLC owns and operates a pilot plant facility in Rifle Colorado.[46]
Hot recycled solids technologies
Hot recycled solids technologies use heat, which is transferred by mixing hot solid particles with the oil shale. These technologies usually process oil shale fines (less than 10 mm). The heat carrier (usually shale ash) is heated by combustion in a separate chamber or vessel, thus the retort vapours are not diluted with combustion exhaust. The main technologies are Alberta Taciuk Process, Galoter, TOSCO II, Lurgi-Ruhrgas, Chevron STB, LLNL HRS, and Shell Spher processes.[40][41] In the Galoter process, retorting takes place in a rotary kiln-type retort and it's possible to use also shale fines. The spent shale is burned in a spouted bed and solid shale ash is used as the heat carrier.[43] In the case of kukersite the yield of crude oil accounts roughly 12% of shale and the oil consists 15-20% of low-boiling fractions. The Galoter process is more environmental-friendly than the Kiviter process, as the water use and pollution is smaller. However, the burning residue causes some environmental problems because of organic carbon and calcium sulphide consistent.[42] The Galoter process is used for oil production by Eesti Energia, Estonian energy company.[44] The company has 2 retorts both processing 125 t/h of oil shale and plans to build 2 more.[47] Another Estonian company, VKG Oil AS, is constructing in 2007/08 a new production line using the Galoter process engineered by Atomenergoproject of St Petersburg[48]
Like the Galoter process, the Alberta Taciuk processes oil shale fines in a rotary kiln-type retort. The unique feature of the Alberta Taciuk is that drying and pyrolysis of the feed shale and combustion, recycling and cooling of the spent shale all occur in a single multi-chamber horizontal, rotating vessel.[49] The produced oil consists up to 30% of low-boiling fractions. The water pollution in the process is quite moderate.[42] Australian oil companies Southern Pacific Petroleum NL and later Queensland Energy Resources operated a 250 t/h industrial-scale pilot plant using the Alberta Taciuk Processor. The plant closed in 2004. UMATAC Industrial Processes is designing the 6000-ton-per-day Alberta Taciuk Processor in China, scheduled for operation in 2008.[50] Estonian VKG Oil is considering construction of new retort using the Alberta Taciuk Processor.[44] Oil Shale Exploration Company LLC has arranged for an exclusive right to license the ATP for research, development and demonstration near Vernal Utah.[51] Like the Galoter and Alberta Taciuk, the TOSCO II also processes oil shale fines that are heated with hot recycled solids in a rotary kiln. However instead of recycling shale ash, the TOSCO II circulates hot ceramic balls between the retort and a heater. The process was tested in a 40 t/h test facility near Parachute Colorado that closed in 1972. The LLNL HRS (hot-recycled-solid) retorting process is worked out by the Lawrence Livermore National Laboratory. The technology was used in a 4-tonne/day pilot plant from 1990 to 1993. A delayed-fall combustor, which is used in this process, gives greater control over the combustion process compared with a lift pipe combustor. A fluidized-bed mixer is used instead of the screw mixer. which is used in the Lurgi process. The majority of the pyrolysis occurs in a settling-bed unit.[40]
Conduction through a wall technologies
Conduction through a wall technologies use heat, which is transferred by conduction through the retort wall. These technologies normally process fines and the retort vapours are not diluted by combustion exhaust. Technologies include Pumpherston, Fischer assay, Hom Tov and Oil-Tech processes.[40][41] Oil-Tech staged electrically heated retort process is developed by Millennium Synfuels, LLC (former Oil Tech Inc.). In this process, the feedstock material is heated to greater degrees as it goes further down the retort. The retort-style prototype was reported to have passed a test.[52] In the Hom Tov process (US Patent 5372708), fine oil shale is slurried with waste bitumen and pumped through coils in a heater. Israeli promoters claim that the technology enables the shale to be processed at somewhat lower temperatures with the addition of the catalyzing bitumen. The technology has not been tested in a pilot plant yet. Fischer Assay is a standardized laboratory test that is used to measure the grade of an oil shale sample. A 100-gram sample crushed to 8-mesh (2.38 mm) screen is heated in a small aluminum retort to 500 °C at a rate of 12 °C per minute, and held at that temperature for 40 minutes.[16] The distilled vapors of oil, gas, and water are passed through a condenser and cooled with ice water into a graduated centrifuge tube. The oil yields achieved by other technologies are often reported as a percentage of the Fischer Assay oil yield.
Externally generated hot gas technologies
Externally generated hot gas technologies or indirectly heated technologies use heat, which is transferred by gases that are heated outside of the retort vessel. The main technologies are Petrosix, Union B, Paraho Indirect, and Superior Indirect processes.[40][41] Like the internal combustion technologies, most of the externally-generated hot gas technologies process oil shale lumps in vertical shaft kilns, however the retort vapours are not diluted with combustion exhaust. The world’s largest surface oil shale pyrolysis reactor currently operating is the Petrosix in São Mateus do Sul, Paraná, Brazil. The 11-m diameter vertical shaft kiln is owned by Petrobras and has being operating since 1992 with high availlability. The company operates 2 retort, the largest of which processes 260 t/h of oil shale. The largest retort ever built used the Union B technology, developed by Unocal. The Union B processed 400 t/h of oil shale lumps heated by externally generated hot gas. However unlike all other vertical shaft kilns, the Union B pumped the oil shale into the bottom of the retort and hot gas entered at the top. Unocal operated the retort from 1986 to 1992 near Parachute, Colorado. The Paraho Indirect technology is similar to the Petrosix which is considered a highly reliable technology for use with U.S. oil shale.[44]
Reactive fluids technologies
Reactive fluids technologies are IGT Hytort (high-pressure H2), and Donor solvent processes.[40] These technologies are more appropriate hydrogen-poor shales, such as the Eastern US Devonian shales, for which only a third of the organic carbon is typically converted to oil during conventional aboveground retorting. The hydrogen or hydrogen donor react with coke precursors and roughly double the yield of oil, depending on the details of the shale and process [R. Rex, J Janks, T. Knowlton, Cold Flow Model Testing of the Hytort Process Retort Design, 17th Oil Shale Symposium. Colo. Sch. Mines Press. pp. 17-36.]
Fluid Bed Reactor
Chattanooga Corp have developed an oil crude extraction method for oil shales, tar sands and other unconventional oil by a fluid bed rector and a associated hydrogen fired heater. At relatively low temperatures(1000 F)through thermal cracking and hydrogenation into hydrocarbon vapors and spent solids. The thermal cracking allows for hydrocarbon vapors to be extracted off the oil shale which is then extracted and scrubbed of solids. The vapor is then cooled, during this cooling condensate drops out of the gas, the remaining hydrogen, light hydrocarbon (HC) and acid gases are passed through an amine scrubbing system to remove hydrogen sulfide which is converted to elemental sulfur. The cleaned hydrogen and light hydrocarbon gases are then fed back into the system for compression or into the hydrogen heater which provide the heat for the fluid bed reactor. This almost closed loop allows for a very efficient process where nearly all the energy needs are provided by the source material and the end result is a valuable light condensate crude. The demonstration plant in Canada was able to produce 51 gal/ton of shale oil at an API gravity between 28-30. With hydrotreating ti would be possible to improve this to 38-40 API. Chattanooga Corp are currently looking at designs o produce a 60,000 b/d facility.[53]
In-situ
The in-situ technologies are usually classified as true in-situ processes (TIS) and modified in-situ processes (MIS). While true in-situ processes do not involve mining the shale, the modified in-situ involves prior to heating mining beneath the target oil shale deposit, and drilling and fracturing the target deposit above the mined area to create void space of 20 to 25 percent to improve the flow of gases and liquid fluids through the rock formation, and by that increasing the volumes and quality of the oil produced.[44] The in-situ technologies could be also classified similarly to the ex-situ classification by the method of heating.
In-situ operations could potentially extract more oil from a given area of land than conventional oil shale mining and retorting, as the wells can reach much deeper than surface strip-mines can. With in-situ processing, the shale is fractured and heated underground to release gases and oils. Several companies have patented methods for in-situ retorting. However, most of these methods are still experimental.
Early In-Situ Methods
A variety of true in-situ processes were tried prior to the oil shale crash in the 1980s. Most notable are the Equity Oil process, which injected superheated steam in the permeable leached zone of Colorado’s Piceance Basin [P. M. Dougan, L. Dockter, “BX In Situ Oil Shale Project,” 14th Oil shale Symposium Proceedings, Colo. Sch. Mines Press, 1981, pp. 118-127], and the Geokinetics Process, which is a horizontal combustion retort in which permeability is formed by explosive uplift and rubblization. [C. E. Tyner, R. L. Parrish, B. H. Major, J. M. Lekas, “Sandia/Geokinetics Retort 23: A Horizontal In Situ Retorting Experiment, 15th Oil shale Symposium Proceedings, Colo. Sch. Mines Press, 1982, pp.370-384.] Little yield information is available from the Equity process, but the Geokinetics process generally recovered 40-50% of the Fischer assay oil.
Variations of the modified in-situ (MIS) process have been investigated by the US Bureau of Mines, Lawrence Livermore National Laboratory, Occidental Petroleum, Rio Blanco Corporation, and Multi-Mineral Corporation. An early concept in the 1960s was to create a rubble chimney using a nuclear explosive.[D. B. Lombard and H. C. Carpenter, “Recovering Oil by Retorting a Nuclear Chimney in Oil Shale,” J. Petroleum Technology 19, 727-734 (1967)] This approach was abandoned for a variety of technical reasons. Subsequently, a variety of conventional mining and rubblization approaches were explored. The first MIS oil shale experiment was conducted by Occidental Petroleum in 1972 at Logan Wash.[44] Oil yield was adversely affected by inefficient sweep of the rubblized zone due to nonuniform permeability. [M. L. Gregg and J. H. Campbell, “Sweep efficiency modeling of modified in-situ retorts” 13th Oil Shale Symposium Proceedings, Colo. Sch. Mines Press, 1980, pp. 87-100] A subsequent series of field experiments tried to improve permeability uniformity by different mining and blasting approaches. Occidental achieved 50-60 %FA oil yield in Retorts 7 and 8, depending on how it is calculated. [T. C. Bickel, “Data Acquisition and Analysis of Occidental Vertical Modified In Situ Retorts 7 and 8, Sandia Report SAND83-2649, 1984] Rio Blanco Corporation used a different mining and blasting approach that created a bed with close to 40% porosity. This enabled them to retort the chimney at a substantially faster rate and achieved higher oil yields—about 70% of Fischer assay. [K. L. Berry, R. L. Hutson, J. S. Sterrett and J. C. Knepper, “Modified In-Situ Retorting Results of Two Field Retorts, 15th Oil shale Symposium Proceedings, Colo. Sch. Mines Press, 1982, pp. 385-396] Multi-Mineral Corporation proposed a more complicated MIS process for Saline Zone oil shale that included recovery of nahcolite and Dawsonite minerals.
Shell's In-Situ Conversion Process (ICP)
The Shell Oil Company has been developing a new method since 2000 under the name the Mahogany Research Project in Colorado, some 200 miles (320 km) west of Denver. This is a true in-situ technology which uses conduction through a wall and reactive fluids (some embodiments) methods for the heating. This method is energy intensive though but favours well when compared to other heavy oil projects like the Tar sands. If a full field project was to be undertaken it is estimated that for every unit of energy consumer 3.5 units would be produced over the project life cycle. It also has the benefit that the hydrocarbons produced is much lighter than traditional crude.
First a freeze wall is constructed to seal off groundwater by drilling 2000' wells, eight feet apart, around the perimeter of a 10 acre working zone, and then circulating with a super-chilled liquid to freeze the ground to -60oF. This freeze wall is present as an environmental measure to prevent contamination of the groundwater. The working zone is then dewatered. Recovery wells are drilled on 40' spacing within the working zone. An electrical heating element is lowered into each well and allowed to heat the kerogen to 650 to 700oF over a period of approximately four years, slowly converting it into oils and gases, which are then pumped to the surface. The company believes that it will be possible to recover in the region of 65-70% of the hydrocarbons in place. An operation producing 100,000 barrels a day would require a dedicated electrical generating capacity of 1.2 gigawatts. To maximize the functionality of the freeze walls, working zones will be developed, in succession, adjacent to each other. This in-situ method requires 100% surface disturbance, greatly increasing the footprint of extraction operations in comparison to conventional oil and gas drilling.[54]
The current test sites are expected to produce in the region of 600 to 1,500 bopd
EGL Resources
EGL Resources proposes a method that combines horizontal wells, through which steam is passed, and vertical wells, which provide both vertical heat transfer through refluxing of generated oil and a means to collect and produce the oil. In contrast to the Equity process, the steam circulates through a closed loop, and no fluids are injected into the formation. Horizontal heat transfer from the vertical wells is similar to that in the Shell ICP, and a similar oil quality is expected. They are currently leasing a 160-acre tract in the Piceance Basin from the US Bureau of Land Management for their tests.[55]
Chevron
Chevron Corporation and Los Alamos National Laboratory formed a joint research project in 2006 to develop oil shale. They have leased a 160 acre patch from the US Bureau of land management for their tests. They are investigating whether CO2 can be injected into the formation at a raised temperature which will decompose the kerogen into conventional hydrocarbons. The CO2 would be injected via conventionally drilled wells and then exposed to the formation via a series of horizontal fractures where it would circulate around. The hydrocarbons would then be produced also via conventional vertical oil wells.
This method is based upon research and trials carried out in the 1950s by Sinclair Oil and Gas company which developed a method using natural and induced fractures between vertical wells to produce the in-situ kerogen. Continental oil and the University of Akron also demonstrated and were issued patents that showed that CO2 was a good carrier gas in helping recover the shale oil.[55]
Petro Probe
Petro probe a subsidiary of Earth Science Search have listened a process involving injecting superheated air in to wells drilled into the oil shale. They are currently in negations with the process patent holder which once complete will allow them to begin a three stage test program to verify the process, the economics and the function ability of a complete working plant. The process involves injecting air which is super heated at the surface into wells drilled into the oil shale. The super-heater air then mixes and melts the in-situ shale oil which is transported back to the surface in the gas which is then cooled and the condensate drop out is collected. The produced gas is then in turned used to heat the air and is injected back with other waste products into the formation there by minimizing the environmental impact.[53]
ExxonMobil Electrofrac
ExxonMobil has been involved in Oil Shale development since the 1960’s and is currently focused on in-situ developments for oil shale. They are concentrating on an in-situ method which heats the oil shale via an electrically conductive heating fluid which has been injected into the reservoir and heats the oil shale via a series of hydraulic fractures. The oil shale is produced by separate dedicated production wells.
It is thought that most likely method is to have horizontal wells which have been hydraulically fractured along the vertical axis. These wells are place in a parallel row with a second horizontal well intersecting them at their toe. This will allow the two different charges to be applied at either end. ExxonMobil is pursuing this method as they believe it provides a better method in which is reach into the surround oil shale and heat it up.
The Electrofrac method has been tested in laboratories and test sites are now currently being considered for a field trial.[53]
Volumetric heating by radio waves technologies
The concept of volumetric heating by radio waves (radio frequency processing) of oil shale was developed at IITRI in the late 1970s. The concept was to heat modest volumes of shale over using vertical electrode arrays. Deeper large volumes could be processed at slower heating rates over a period. The technology was developed later by the Lawrence Livermore National Laboratory (LLNL), and by several other inventors. The LLNL concept based on the use of wells spaced at tens of meters to heat cubic kilometers of deep oil shale very slowly. The concept presumed a radio frequency at which the skin depth is many tens of meters, and thereby overcoming the thermal diffusion times needed for conductive heating.[40][10]
Other uses
Oil shale is or could be used for production of different products like specialty carbon fibers, adsorbent carbons, carbon black, cement, bricks, construction and decorative blocks, soil additives, fertilizers, rock wool insulating material, glass, and pharmaceutical products. However, oil shale usage for production of these products are still small or even in experimental stages only.[16][37]
Some oil shales could be used for uranium and other rare chemical element production. In 1946-1952, a marine type of Dictyonema shale was used for uranium production in Sillamäe, Estonia, and in 1950-1989 alum shale was used in Sweden for the same purpose.[16] Oil shale gas could be used as a substitute for natural gas, however at the current price level this is not economically feasible.[56][31]
Economics

According to the survey conducted by the RAND, a surface retorting complex (mine, retorting plant, upgrading plant, supporting utilities, and spent shale reclamation) is unlikely to be profitable unless real crude oil prices are at least US$70 to US$95 per barrel.[36] Once commercial plants are in operation and experience-based learning takes place, costs are expected to decline to US$35–US$48 per barrel after 12 years. After production of 1000 million barrels, costs are estimated to decline further to $30 – $40 per barrel.[57] In 2005, Royal Dutch Shell announced that its in situ extraction technology deployed in Colorado could be competitive at prices over US$30 per barrel.[58] However, it is possible that the real competitive price level will be higher as the costs for building an underground wall of frozen water to contain melted shale have significantly escalated.[59]
At the full scale production, the production costs for one barrel of light crude oil of the Australia's Stuart plant were projected to be in the range of US$11.3 to $12.4 per barrel, including capital costs and operation costs at a 30 years projected lifetime. However, the project is suspended due environmental concerns.[57][60] Israel's AFSK Hom Tov process, which produces oil from a mixture of oil refinery residue (in the form of bitumen) and oil shale, claims to be profitable at US$16-US$17 per barrel. This technology still being tested.
The project of a new ATP retort planned by VKG Oil, is estimated to achieve break-even financial feasibility operating at 30% capacity, assuming a crude oil price of US$21 per barrel or higher. At 50% utilization, the project is economic at a price of US$18 per barrel, while at full capacity, it could be economic at price of US$13 per barrel.[44]
Due to the low price of oil and other competitive fuels, oil shale production has ceased in Canada, Scotland, Sweden, France, Australia, Romania and South Africa, and has not taken off in the USA, Belarus, Jordan and Morocco.[9] During the oil crisis of the 1970s, people thought that oil supplies were peaking, expected oil prices to be around seventy dollars a barrel for some time to come, and invested huge amounts of money in refining oil shale — money that they lost. Because of the huge losses last time around, there is considerable reluctance to invest in shale oil production. Investors are waiting to see if oil prices really will remain in high level and no hurry to develop oil shale. However, USA, Canada and Jordan are planning or already started with test projects, and Australia considers restarting oil shale production.[9][33]
Company | Location | Method | Status |
---|---|---|---|
Petrobras | Sao Mateus do Sul, Brazil | Externally generated hot gas (Petrosix process) | Operational |
Shell Frontier Oil and Gas | Colorado, USA | True in-situ process (ICP) | Pilot project |
ExxonMobil | Colorado, USA | Modified in-situ process; reactive fluids | pilot project |
Chevron Shale Oil Company | Colorado, USA | Modified in-situ process | Pilot project |
EGL Resources | Colorado, USA | True in-situ process | Pilot project |
Millennium Synfuels | Utah, USA | Staged electrically heated retort process | Pilot project |
Oil Shale Exploration | Utah, USA | ATP | Pilot project |
Shale Technologies LLC | Rifle, Colorado, USA | Internal combustion (Paraho Direct process) | Pilot project |
Queensland Energy Resources | Stuart Deposit, Queensland, Australia | Hot recycled solids (ATP) | Pilot project |
Fushun Mining Group | Fushun, China | Internal combustion (Fushun process) | Operational |
VKG Oil | Kohtla-Järve, Estonia | Internal combustion (Kiviter process) | Operational |
Eesti Energia | Narva, Estonia | Hot recycled solids (Galoter process) | Operational |
Kiviõli Keemiatööstus | Kiviõli, Estonia | Internal combustion (Kiviter process) | Operational |
A critical measure of the viability of oil shale is the ratio of energy used to produce the oil, compared to the energy returned (Energy Returned on Energy Invested - EROEI). Generally, the oil shale has to be mined, transported, retorted, and then disposed of, so at least 40% of the energy value is consumed in production. EROEI of the different oil shale deposits varies between 0.7-13.3.[14] Royal Dutch Shell has reported a figure of EROEI about 3:1 on its recent in-situ development, Mahogany Research Project, which uses electric heating of the shale up to 500 degrees Fahrenheit (260 °C. This compares to a figure of typically 5:1 for conventional oil extraction. EROEI may be less important if alternate energy sources are used to fund the process.
Water is also needed to add hydrogen to the oil-shale oil before it can be shipped to a conventional oil refinery. The largest deposit of oil shale in the United States is in western Colorado (the Green River Shale deposits), a dry region with no surplus water. The oil shale can be ground into a slurry and transported via pipeline to a more suitable pre-refining location.
Several co-pyrolysis processes to increase efficiency of oil shale retorting have been proposed or tested. In Estonia, the co-pyrolysis of kukersite with renewable fuel (wood waste), as also with plastic and rubber wastes (tyres) has been tested.[61] Co-pyrolysis of oil shale with high-density polyethylene (HDPE) has been tested also in Morocco and Turkey.[62][63] Israel's AFSK Hom Tov co-pyrolysis oil shale with oil refinery residue (bitumen). Some tests involve co-pyrolysis of oil shale with lignite and cellulose wastes. Depending on reaction conditions the co-pyrolysis may lead to higher conversion ratio and thus lower production costs, and in some cases solves the problem of utilization of certain wastes.[61]
Environmental considerations
Oil shale industry has a number of environmental impacts due to the energy intensive nature of extracting and processing. It can leave environmental footprints on the land, atmospherically and in the groundwater, if the risks are not managed correctly. Opposition to to one oil shale program as resulted in it being put on hold in Australia. [64]
Surface-mining of oil shale deposits has all the environmental impacts of open-pit mining. In addition, the combustion and thermal processing generate waste material, which must be disposed of, and atmospheric emissions, including carbon dioxide, a major greenhouse gas. Experimental in-situ conversion processes and carbon capture and storage technologies may reduce some of these concerns in future, but may raise others, such as the pollution of groundwater.[65]
See also
- Oil reserves
- Non-conventional oil
- Tar sands
- Future energy development
- Abiogenic petroleum origin
- Mahogany research project
- Bituminous coal
- Synthetic Liquid Fuels Program
- Bituminous rocks
- Coal oil
- Green River Basin
- World energy resources and consumption
- Core research center
- Mitigation of peak oil
Footnotes
- ^ WEC, p. 73
- ^ a b Alali, Jamal; Abu Salah, Abdelfattah; Yasin, Suha M.; Al Omari, Wasfi (2006), Oil Shale in Jordan (PDF), Natural Resources Authority of Jordan, retrieved 2007-06-29
- ^ a b Yin, Liang (7-9 November 2006). "Current status of oil shale industry in Fushun, China" (PDF). Amman, Jordan. Retrieved 2007-06-29.
{{cite journal}}
: Check date values in:|date=
(help); Cite journal requires|journal=
(help) - ^ a b WEC, p. 81-82
- ^ "Annual Energy Outlook 2006" (PDF). Energy Information Administration. February 2006. Retrieved 2007-06-22.
{{cite journal}}
: Check date values in:|date=
(help); Cite journal requires|journal=
(help) - ^ Andrews, Anthony (13 April 2006), Oil Shale: History, Incentives, and Policy (PDF), Congressional Research Service, retrieved 2007-06-25
{{citation}}
: Check date values in:|date=
(help) - ^ "NPR's National Strategic Unconventional Resource Model" (PDF). United States Department of Energy. April 2006. Retrieved 2007-07-09.
{{cite journal}}
: Check date values in:|date=
(help); Cite journal requires|journal=
(help) - ^ Robert Rapier (2006-06-12). "Oil Shale Development Imminent". R-Squared Energy Blog. Retrieved 2007-06-22.
{{cite journal}}
: Check date values in:|date=
(help); Cite journal requires|journal=
(help) - ^ a b c d e f g h i Brendow, K. (2003). "Global oil shale issues and perspectives. Synthesis of the Symposium on Oil Shale. 18-19 November, Tallinn" (PDF). Oil Shale. A Scientific-Technical Journal. 20 (1). Estonian Academy Publishers: 81–92. ISSN 0208-189X. Retrieved 2007-07-21.
- ^ a b c A. K. Burnham (2003-08-20). "Slow Radio-Frequency Processing of Large Oil Shale Volumes to Produce Petroleum-like Shale Oil" (PDF). Lawrence Livermore National Laboratory. UCRL-ID-155045. Retrieved 2007-06-28.
{{cite journal}}
: Check date values in:|date=
(help); Cite journal requires|journal=
(help) - ^ Greenpeace Australia Pacific (2005-03-03). "Climate-changing shale oil industry stopped". Retrieved 2007-06-28.
{{cite web}}
: Check date values in:|date=
(help) - ^ WEC, p. 74
- ^ a b c d Altun, N. E.; Hiçyilmaz, C.; Hwang, J.-Y.; Suat Bağci, A.; Kök, M. V. (2006). "Oil Shales in the world and Turkey; reserves, current situation and future prospects: a review" (PDF). Oil Shale. A Scientific-Technical Journal. 23 (3). Estonian Academy Publishers: 211–227. ISSN 0208-189X. Retrieved 2007-06-16.
{{cite journal}}
: Check date values in:|year=
(help)CS1 maint: year (link) - ^ a b c Lee, Sunggyu (1990). Oil Shale Technology. CRC Press. p. 10. ISBN 0849346150. Retrieved 2007-07-09.
{{cite book}}
: Check date values in:|year=
(help)CS1 maint: year (link) Cite error: The named reference "science" was defined multiple times with different content (see the help page). - ^ Hutton, A.C. (1987), "Petrographic classification of oil shales", International Journal of Coal Geology, 8, Elsevier Science: 203–231, ISSN 0166-5162
{{citation}}
: Check date values in:|year=
(help)CS1 maint: year (link) - ^ a b c d e f g h i j k l m n o p q r Dyni, John R. (2006). "Geology and resources of some world oil-shale deposits. Scientific Investigations Report 2005–5294" (PDF). U.S. Department of the Interior. U.S. Geological Survey. Retrieved 2007-07-09.
{{cite journal}}
: Check date values in:|year=
(help); Cite journal requires|journal=
(help)CS1 maint: year (link) - ^ J. J. Sweeney, A. K. Burnham, R. L. Braun, “A Model of Hydrocarbon Generation from Type I Kerogen: Application to Uinta Basin,” AAPG Bulletin 71, 967-985 (1987)
- ^ WEC, p. 77
- ^ WEC, p. 80
- ^ a b c Qian, J.; Wang, J.; Li, S. (2003). "Oil Shale Development in China" (PDF). Oil Shale. A Scientific-Technical Journal. 20 (3). Estonian Academy Publishers: 356–359. ISSN 0208-189X. Retrieved 2007-06-16.
{{cite journal}}
: Check date values in:|year=
(help)CS1 maint: year (link) - ^ a b c Hamarneh, Yousef (1998; 2006). "Oil Shale Resources Development In Jordan" (PDF). Amman: Natural Resources Authority of Jordan. Retrieved 2007-06-16.
{{cite journal}}
: Check date values in:|date=
(help); Cite journal requires|journal=
(help); Unknown parameter|coauthors=
ignored (|author=
suggested) (help) - ^ WEC p. 88
- ^ WEC p. 91
- ^ WEC p. 84-85
- ^ WEC p. 83-84
- ^ a b Laherrère, Jean (2005). "Review on oil shale data" (PDF). Hubbert Peak. Retrieved 2007-06-17.
{{cite journal}}
: Check date values in:|date=
(help); Cite journal requires|journal=
(help) - ^ Russell, Paul L. (1990), Oil shales of the world, their origin, occurrence and exploitation (First ed.), Pergamon Press, pp. 162–224, ISBN 9780080372402
{{citation}}
: Check date values in:|year=
(help)CS1 maint: year (link) - ^ a b c d e f g h i j k WEC, p. 75-77
- ^ "Non-Nuclear Energy Research in Europe – A comparative study. Country Reports A – I. Volume 2" (PDF). European Commission. Directorate-General for Research. 2005. EUR 21614/2. Retrieved 2007-06-29.
{{cite journal}}
: Check date values in:|date=
(help); Cite journal requires|journal=
(help) - ^ Dr. James H. Gary, Editor (August 1979). "Twelfth Oil Shale Symposium Proceedings" (PDF). Colorado School of Mines Press. Retrieved 2007-06-02.
{{cite journal}}
:|author=
has generic name (help); Cite journal requires|journal=
(help) - ^ a b Ingo Valgma. "Map of oil shale mining history in Estonia". Mining Institute of Tallinn Technical University. Retrieved 2007-07-21.
- ^ "History of the company". Viru Keemia Grupp. Retrieved 2007-07-21.
- ^ a b "Shale oil. AIMR Report 2006". Geoscience Australia. Retrieved 2007-05-30.
- ^ "Nominations for Oil Shale Research Leases Demonstrate Significant Interest in Advancing Energy Technology. Press release". Bureau of Land Management. 2005-09-20. Retrieved 2007-07-10.
- ^ "What's in the Oil Shale and Tar Sands Leasing Programmatic EIS". Oil Shale and Tar Sands Leasing Programmatic EIS Information Center. Retrieved 2007-07-10.
- ^ a b Bartis, James T.; LaTourrette, Tom; Dixon, Lloyd; Peterson, D.J.; Cecchine, Gary (2005). "Oil Shale Development in the United States. Prospects and Policy Issues. Prepared for the National Energy Technology Laboratory of the U.S. Department of Energy" (PDF). The RAND Corporation. ISBN 978-0-8330-3848-7. Retrieved 2007-06-29.
{{cite journal}}
: Check date values in:|date=
(help); Cite journal requires|journal=
(help) - ^ a b WEC, p 85-90
- ^ Liblik, V.; Kaasik, M.; Pensa, M.; Rätsep, A.; Rull, E.; Tordik, A. (2006), "Reduction of sulphur dioxide emissions and transboundary effects of oil shale based energy production" (PDF), Oil Shale. A Scientific-Technical Journal, 23 (1), Estonian Academy Publishers: 29–38, ISSN 0208-189X, retrieved 2007-06-16
- ^ Qian, Jialin; Wang, Jianqiu (7-9 November 2006). "World oil shale retorting technologies" (PDF). Amman, Jordan. Retrieved 2007-06-29.
{{cite journal}}
: Check date values in:|date=
(help); Cite journal requires|journal=
(help) - ^ a b c d e f g h i Burnham, Alan K.; McConaghy, James R. (16–18 October 2006), Comparison of the Acceptability of Various Oil Shale Processes (PDF), Golden: 26th Oil Shale Symposium, UCRL-CONF-226717, retrieved 2007-06-23
{{citation}}
: CS1 maint: date format (link) - ^ a b c d "An Assessment of Oil Shale Technologies" (PDF). June 1980. NTIS order #PB80-210115.
{{cite journal}}
: Check date values in:|date=
(help); Cite journal requires|journal=
(help) - ^ a b c Mölder, Leevi (2004). "Estonian Oil Shale Retorting Industry at a Crossroads" (PDF). Oil Shale. A Scientific-Technical Journal. 21 (2). Estonian Academy Publishers: 97–98. ISSN 0208-189X. Retrieved 2007-06-23.
{{cite journal}}
: Check date values in:|date=
(help) - ^ a b Soone, Jüri; Riisalu, Hella; Kekisheva, Ljudmilla; Doilov, Svjatoslav (7–9 November 2006), Environmentally sustainable use of energy and chemical potential of oil shale (PDF), Amman, Jordan, retrieved 2007-06-29
{{citation}}
: CS1 maint: date format (link) CS1 maint: location missing publisher (link) - ^ a b c d e f g "Strategic Significance of America's Oil Shale Resource. Volume II Oil Shale Resources, Technology and Economics" (PDF). Office of Deputy Assistant Secretary for Petroleum Reserves; Office of Naval Petroleum and Oil Shale Reserves; U.S. Department of Energy. 2004. Retrieved 2007-06-23.
{{cite journal}}
: Check date values in:|date=
(help); Cite journal requires|journal=
(help) - ^ Purga, Jaanus (2004), "Today's rainbow ends in Fushun" (PDF), Oil Shale. A Scientific-Technical Journal, 21 (4), Estonian Academy Publishers: 269–272, ISSN 0208-189X, retrieved 2007-06-23
- ^ "Shale Technologies". Shale Technologies, LLC. Retrieved 2007-06-24.
- ^ Liive, Sandor (2007), "Oil Shale Energetics in Estonia" (PDF), Oil Shale. A Scientific-Technical Journal, 24 (1), Estonian Academy Publishers: 1–4, ISSN 0208-189X, retrieved 2007-06-24
- ^ "New shale oil line for VKG Oil AS" (PDF), Rintekno Newsletter, 20, Rintekno Oy, 2006, retrieved 2007-06-24
- ^ "Technology Details: Alberta Taciuk Process". aboutREMEDIATION. Retrieved 2007-06-24.
- ^ Chandler, Graham (2006), "US eyes Alberta as model for developing oil shale" (PDF), Alberta Oil, 2 (4): 16–18, retrieved 2007-06-24
- ^ "OSEC's Process: A Proven Technology". Oil Shale Exploration Company, LLC. Retrieved 2007-06-24.
- ^ Fischer, Perry A. (2005), "Hopes for shale oil are revived", World Oil, 226 (8), retrieved 2007-06-24
- ^ a b c DOE (2007), Secure Fuels from Domestic Resources:The Continuing Evolution of America’s Oil Shale and Tar Sands Industries (PDF), pp. 1–68, retrieved 2007-07-11
- ^ "Oil Shale Test Project. Oil Shale Research and Development Project" (PDF). Shell Frontier Oil and Gas Inc. 2006-02-15. Retrieved 2007-06-30.
{{cite journal}}
: Cite journal requires|journal=
(help) - ^ a b "Innovation in Shale Technology" (website). EGL Shale. 2006-11-16. Retrieved 2007-07-06.
{{cite journal}}
: Cite journal requires|journal=
(help) Cite error: The named reference "EGLl" was defined multiple times with different content (see the help page). - ^ Schora, F. C.; Tarman, P. B.; Feldkirchner, H. L.; Weil, S. A. (1976), "Hydrocarbon fuels from oil shale", Proceedings, 1, American Institute of Chemical Engineers: 325–330, A77-12662 02-44
{{citation}}
: Check date values in:|year=
(help)CS1 maint: year (link) - ^ a b "A study on the EU oil shale industry viewed in the light of the Estonian experience (IP/A/ITRE/FWC/2005-60/SC4)" (PDF). European Parliament. October 2006. Retrieved 2007-06-02.
{{cite journal}}
: Check date values in:|date=
(help); Cite journal requires|journal=
(help) - ^ Linda Seebach (2 September 2005). "Shell's ingenious approach to oil shale is pretty slick". Rocky Mountain News. Retrieved 2007-06-02.
- ^ Nancy Lofholm (16 June 2007). "Shell shelves oil-shale application to refine its research". The Denver Post. Retrieved 2007-06-24.
- ^ Schmidt, S. J. (2003), "New directions for shale oil:path to a secure new oil supply well into this century: on the example of Australia" (PDF), Oil Shale. A Scientific-Technical Journal, 20 (3), Estonian Academy Publishers: 333–346, ISSN 0208-189X, retrieved 2007-06-02
- ^ a b Veski, R.; Palu, V.; Kruusement, K. (2006), "Co-liquefaction of kukersite oil shale and pine wood in supercritical water" (PDF), Oil Shale. A Scientific-Technical Journal, 23 (3), Estonian Academy Publishers: 236–248, ISSN 0208-189X, retrieved 2007-06-16
- ^ Aboulkas, A.; El Harfi, K.; El Bouadili, A.; Benchanaa, M.; Mokhlisse, A.; Outzourit, A. (2007), "Kinetics of co-pyrolysis of Tarfaya (Morocco) oil shale with high-density polyethylene" (PDF), Oil Shale. A Scientific-Technical Journal, 24 (1), Estonian Academy Publishers: 15–33, ISSN 0208-189X, retrieved 2007-06-16
- ^ Ozdemir, M.; Akar, A.; Aydoğan, A.; Kalafatoglu, E.; Ekinci, E. (7–9 November 2006), Copyrolysis of Goynuk oil shale andthermoplastics (PDF), Amman, Jordan, retrieved 2007-06-29
{{citation}}
: CS1 maint: date format (link) CS1 maint: location missing publisher (link) - ^ Greenpeace Australia Pacific (2005-03-03). "Climate-changing shale oil industry stopped". Retrieved 2007-06-28.
{{cite web}}
: Check date values in:|date=
(help) - ^ Jim Bartis, RAND Corporation (2006). "Unconventional Liquid Fuels Overview. 2006 Boston World Oil Conference" (PDF). Association for the Study of Peak Oil & Gas - USA. Retrieved 2007-06-28.
{{cite journal}}
: Check date values in:|date=
(help); Cite journal requires|journal=
(help)
References
- Survey of energy resources (PDF) (20 ed.). World Energy Council (WEC). 2004. ISBN 9780080444109. Retrieved 2007-07-20.
{{cite book}}
: Check date values in:|date=
(help)
External links

- Oil Shale. A Scientific-Technical Journal. Estonian Academy Publishers. ISSN 0208-189X
- Selected online oil shale publications by the U.S. Geological Survey
- Oil Shale: Toward a Strategic Unconventional Fuels Supply Policy, by Daniel Fine, Ph.D.Heritage Foundation March 8, 2007
- WorldOil.com - Oil shale back in the picture
- Statement Of Thomas Lonnie Assistant Director for Minerals, Realty & Resource Protection, Bureau of Land Management, U.S. Department of the Interior before the Senate Energy and Natural Resources Committee Oversight Hearing on Oil Shale Development Efforts, Bureau of Land Management, April 12, 2005
- "The Scandinavian Alum Shales" by Astrid Andersson, Bertil Dahlman, David G. Gee and Sven Snall, 1985 ISBN 91-7158-334-3
- 27th Oil Shale Symposium
- Estonian oil shale